Neither the whole or any part of the
information contained in, or the product described in, this manual may be
adapted or reproduced in any material form except with the prior written
approval of Acorn Computers Limited (Acorn Computers).
The product described in this manual and
products for use with it, are subject to continuous developments and
improvement. All information of a technical nature and particulars of the
product and its use (including the information in this manual) are given by
Acorn Computers in good faith. However, it is acknowledged that there may be
errors or omissions in this manual. A list of details of any amendments or
revisions to this manual can be obtained upon request from Acorn Computers
Technical Enquiries. Acorn Computers welcome comments and suggestions relating
to the product and this manual.
All correspondence should be addressed
to:
Technical
Enquiries
Acorn
Computers Limited
Fulbourn
Road
Cherry
Hinton
Cambridge
CB1
4JN
All maintenance and service on the product
must be carried out by Acorn Computers’ authorised dealers. Acorn
Computers can accept no liability whatsoever for any loss or damage caused by
service or maintenance by unauthorised personnel. This manual is intended only
to assist the reader in the use of the product, and therefore Acorn Computers
shall not be liable for any loss or damage whatsoever arising from the use of
any information or particulars in, or any error or omission in, this manual, or
any incorrect use of the product.
BBC Microcomputer Service
Manual
Contents
IMPORTANT: The wires in the mains lead for the
computer are coloured in accordance with the following
code:
Green and yellow - Earth
Blue - Neutral
Brown - Live
As the colours of the wires may not correspond
with the coloured markings identifying the terminals in your plug, proceed as
follows:
The wire which is coloured green and yellow
must be connected to the terminal in the plug which is marked by the letter E,
or by the safety earth symbol or coloured green, or green and
yellow.
The wire which is coloured blue must be
connected to the terminal which is marked with the letter N, or coloured
black.
The wire which is coloured brown must be
connected to the terminal which is marked with the letter L, or coloured
red.
If the socket outlet available is not suitable
for the plug supplied, the plug should be cut off and the appropriate plug
fitted and wired as previously noted. The moulded plug which was cut off should
be disposed of as it would be a potential shock hazard if it were to be plugged
in with the cut off end of the mains cord exposed.
The moulded plug must be used with the fuse
and fuse carrier firmly in place. The fuse carrier is of the same basic colour*
as the coloured insert in the base of the plug. Different manufacturers’
plugs and fuse carriers are not interchangeable. In the event of loss of the
fuse carrier, the moulded plug MUST NOT be used. Either replace the moulded plug
with another conventional plug wired as previously described, or obtain a
replacement fuse carrier from an authorised BBC Microcomputer dealer. In the
event of the fuse blowing it should be replaced, after clearing any faults, with
a 3 amp fuse that is ASTA approved to
BS1362.
This computer was designed and manufactured to
comply with BS 415. In order to ensure the continued safety of Acorn products,
power supplies should be returned to Acorn for repair.
Do not use the Microcomputer in conditions of
extreme heat, cold, humidity or dust or in places subject to vibration. Do not
block ventilation under or behind the computer. Ensure that no foreign objects
are inserted through any openings in the Microcomputer.
*Not necessarily the same shade of that
colour.
1.1 Nature and Purpose of the
Manual
The purpose of this manual is to provide
technical and diagnostic information about the BBC
Microcomputer.
After giving general information about the
technical specification and the mechanical assembly of the BBC Microcomputer, it
gives a detailed description of the operation of the whole of the circuit.
Information is also given about how to upgrade the various models of
microcomputer and the purpose of the various links on the circuit board. Some
details are also given of the ways in which the circuit has changed in its
evolution from issue 1 up to issue 7. There is some guidance about servicing and
fault-finding, further information about interfacing and a few suggestions about
possible applications. Finally there is a section of hardware hints and tips
which is a compilation of ideas from various
sources.
1.2 Technical Specification
The BBC Microcomputer is supplied with two
levels of hardware provision, designated, model A and model B, the former being
fully upgradable to the
latter.
1.2.1 Model A Specification
A fast, powerful self-contained computer
system generating high resolution colour graphics and capable of synthesising 3
part music + 1 channel of noise. The computer is contained in a rigid injection
moulded thermoplastic case. The following are contained within the computer thus
ensuring the minimum of connecting wires.
- 73 key full travel
QWERTY keyboard including 10 user
definable function keys. The keyboard has two key rollover and auto
repeat.
- Internal power supply is fully encased and
manufactured to BS 415 Class 1.
- The internal loudspeaker is driven from a
4-channel sound synthesis circuit with full ADSR envelope
control.
- A colour television signal, for connection to a
normal domestic television aerial socket, is available through a phono
connector. This signal is 625 line, 50Hz, interlaced, fully encoded PAL and is
modulated on UHF channel 36.
- A BNC connector supplies a composite video
output to drive a black and white or PAL colour monitor.
- A standard audio cassette recorder can be used
to record computer programs and data at 300 or 1200 baud using the Computer
Users Tape Standard tones. The cassette recorder is under full automatic motor
control and is connected to the computer via a 7 pin DIN
connector.
- An interrupt driven elapsed time clock enables
real-time control and timing of user responses.
- The unit uses a 2 MHz 6502A and includes 16K of
Random Access Memory.
- A 16K Read Only Memory (ROM) integrated circuit
contains a Machine Operating System designed to interface easily to high level
languages.
- A further 16K Language ROM contains a fast
BASIC interpreter. The interpreter includes a 6502 assembler which enables BASIC
statements to be freely mixed with 6502 assembly language.
- Up to four 16K "sideways" ROMs may be plugged
into the machine at any time. These four ROMs are "paged" and may include
Pascal, word processing, computer aided design software, disc and Econet filing
systems or Teletext acquisition software.
- The full-colour Teletext display of 40
characters by 25 lines, known as mode 7, has character rounding, with double
height, flashing, coloured background and text plus pixel graphics – all
to the Teletext standard.
- The non-Teletext display modes (modes 0 to 6)
provide user definable characters in addition to the standard upper and lower
case alpha-numeric font. In these modes, graphics may be freely mixed with text.
Text characters can be positioned not only on, for example, a 40 x 32 grid, but
at any intermediate position.
- Separate or overlapping text and graphic
windows can be easily user-defined over any area of the display. Each of these
windows may be filled separately and the text window scrolls independently of
the rest of the screen.
- The Model A is able to support the following
modes:–
Mode 4: 320
x 256, 2 colour graphics and 40 x 32 text
(10K)
Mode 5: 160 x 256, 4 colour
graphics and 20 x 32 text (10K)
Mode
6: 40 x 25, 2 colour text only
(8K)
Mode 7: 40 x 25, Teletext
display (1K)
- All graphics access is "transparent" (see
section 2.2), resulting in a fast, snow-free display.
- Extensive support is provided in the Machine
Operating System for the graphics facilities, and this is reflected in the BASIC
interpreter. These facilities include the ability to draw lines very rapidly and
to fill large areas of colour. In addition, very rapid changes of areas of
colour can be effected by the use of a colour "palette”.
- The Model A BBC Microcomputer can be expanded
at any time to the Model B. In addition, or as an alternative, other facilities
such as the Econet may be fitted within the computer
system.
1.2.2 Model B
Specification
The Model B BBC Microcomputer is an enhanced
version of the Model A Microcomputer with the following
differences:–
- 32K Random Access Memory (RAM). This enables
the following extra graphics modes to be
used:–
Mode 0: 640
x 256, 2 colour graphics and 80 x 32 text
(20K)
Mode 1: 320 x 256, 4 colour
graphics and 40 x 32 text (20K)
Mode
2: 160 x 256, 16 colour graphics and 20 x 32 text
(20K)
Mode 3: 80 x 25, 2 colour text
only (16K)
- The installed RAM is divided between the high
resolution graphics display, the user's program and Machine Operating System
variables. If higher resolutions are required with large programs, then the
second processor option may be fitted.
- 6 pin DIN connector provides separate RGB and
sync outputs at TTL levels. RGB are all high true, and sync is link selectable
as high or low true, pulse duration 4.7 microseconds.
- Serial interface to RS423 standard. The new
standard has been designed to be inter-operable with RS232C equipment but offers
a considerably enhanced specification – for example in maximum length of
cable and maximum data transfer rates. Baud rates are software selectable
between 75 baud and 9600 baud. The interface provides not only two-way data
transfer, but also two-way hand-shaking using RTS and CTS lines. The software
for implementing this interface is only provided with operating systems 1.2
onwards.
- An 8 bit input/output port with 2 control bits
is also provided.
- Four analogue input channels are provided. Each
channel has an input voltage range of 0 – 1.8V. The conversion time for
each channel is 10 milliseconds. These analogue inputs can be used not only as
inputs for games-paddles or joysticks but also in laboratory control situations.
The resolution of the ADC chip is 12 bits, but its conversion is such that only
9 or 10 bits are significant. However with suitable averaging, this can be
extended to the full 12 bits accuracy.
- A 1 MHz buffered extension bus is provided for
connection to a variety of external hardware such as a Teletext acquisition
unit, IEEE 488 interface, Winchester disc drive
etc.
1.2.3
Expansion
The following expansion options are available,
some of which may be fitted internally at purchase, but all of which could be
fitted by Dealers at a later date:–
- Floppy disc interface (fitted as an option at
purchase)
- Econet network interface (fitted as an option
at purchase)
- Voice synthesis circuit with cartridge ROM pack
interface
* Various
alternative high-level languages in ROM
External options which plug directly into the
machine include: –
* Games paddles
- Cassette Recorder
- Black and White and colour monitors and
televisions
- 5 1/4” disc drives, ranging from
single-sided single density (100K) to dual double sided double track density
(800K).
- Dot-matrix or daisy wheel printers, serial or
parallel interface
- Teletext acquisition unit enabling
Tele-software to be downloaded into the BBC Computer as well as providing access
to the normal Teletext services. Pages may be "grabbed" and stored for later
use.
- 3 MHz 6502 second processor with 64K of
RAM.
- Z80 second processor with 64K of RAM and a
fully CP/M-compatible operating system.
- IEEE interface
- Winchester 10 megabyte disc
drive
1.2.4 Software
Considerable attention has been paid to the
overall design of both systems and applications software. A modular approach has
been adopted specifically to ease the interfacing of various high-level
languages (such as BASIC and Pascal) to the operating
system.
1.2.5 Machine Operating
System
A 16K ROM is used for the MOS. This software
controls all input/output devices using a well defined interface. The MOS
supports the following interrupts (the full implementation only being available
from MOS 1.2 onwards):–
- Event Timer (10ms) (used as an elapsed time
clock)
- 4 channel analogue to digital
converter
* Vertical
sync
- Keyboard and keyboard buffer
- Music tone generation and
buffer
- Serial interface, input and output
buffers
- Parallel input/output
port
and 'hooks' are
provided to support other devices such as:–
* Teletext acquisition
- Prestel acquisition
- Econet file system
- Disk file
system
* Byte transfer to
second processor
The majority of the operating system calls are
vectored to enable the user to change them if required.
1.2.6
BASIC
The BASIC interpreter is an extremely fast
implementation, with numerous powerful extensions:–
* Long variable names
- Integer, floating point and string
variables
- Multi-dimension integer, floating point and
string arrays
- Extensive support for string
handling
- IF ... THEN ... ELSE
- REPEAT ... UNTIL
- Multi-line integer, floating point and string
functions
- Procedures
- Local variables
- Full recursion on all functions and
procedures
- Effective error trapping and
handling
- Cassette loading and saving of programs and
data
- Full support for the extensive colour graphics
facilities
- Easy control of the built-in music generation
circuits
* Built-in 6502
mnemonic assembler enabling BASIC and assembler to be mixed, or pure assembly
language programs to be
produced.
1.3 Packaging
The BBC Microcomputer is supplied in a two
part moulded polystyrene packing which is further packaged within a cardboard
sleeve. With the Microcomputer, a User's Manual, a Welcome Cassette package and
a UHF TV lead are also supplied. The packaging should be kept intact in case it
becomes necessary to transport the unit at a later
date.
1.4 Mechanical assembly of case
etc
The lid of the Microcomputer case may be
removed after undoing four fixing screws, two on the rear panel and two
underneath. When reassembling, press the lid down at the rear whilst tightening
the two rear fixing screws. Take care not to lose the two spire clips pushed
onto the case lid, into which the rear fixing screws locate. NB Do not remove
the lid with the mains power connected.
Inside the Microcomputer are three main
sub-assemblies:
power supply unit,
keyboard and the main printed circuit board.
To remove the keyboard, undo the two or, in
some cases, three screws and nuts holding it to the case bottom, take care to
note the positions of the associated washers. Unplug the 17 way keyboard
connector and the 2-way loudspeaker connector from the main printed circuit
board, and the 10 way serial-ROM connector, if fitted.
The power supply unit is connected to the main
circuit board by seven push-on connectors which may be unplugged. Three screws
on the underside of the case are undone allowing the unit to be removed. On
reassembly, ensure that the same type of screw is used.
The main printed circuit board can be removed
after the two wires to SK2 (composite video BNC socket) have been disconnected.
Undo the four fixing screws (five or seven screws on later issue boards) and
remove the circuit board from the case by sliding it forwards and then lifting
it from the rear.
2 General
Description of Hardware
2.1 Introduction
This next section gives a general description
of the hardware of the computer, and reference is made to the functional block
diagram (section 9.1) which is laid out approximately as the components are
situated on the printed circuit board. General areas and component orientations
are referred to by using compass points, as shown on the block diagram. When any
reference needs to be made to the specific position of a component, then X-Y
co-ordinates will be used, giving the distances in millimetres from the SW
corner. This is also shown on the block diagram. A list is given in section 8 of
this manual of all the integrated circuits, transistors, diodes, capacitors,
resistors and selection links by number, including their X-Y co-ordinates on the
PCB and on the main circuit diagram.
As each section of the hardware is described,
reference is made to sections of the following chapter in which more detailed
descriptions are given. The heart of the hardware is the 6502 microprocessor,
and in this general description we shall move around the 6502 in an
anti-clockwise direction starting from the SE corner of the
PCB.
2.2 Hardware description
The 6502 accesses an area of just less than 32
Kbytes of ROM. (3/4K of this memory allocation is actually used for
memory-mapped input/output.) The ROM is arranged in such a way that one group of
16K bytes forms a fixed part of the memory map (15 1/4K ROM for the operating
system + 3/4K of I/O), whilst the other 16K has been organised to give as much
flexibility as possible. There is a ROM select facility for accessing up to 16
different memory devices, although only four sideways ROM sockets are available
on the PCB. It is expected that the normal way in which these four sockets will
be used is to provide 2 MHz access to each of 4 chips which could be either 16K
or 8K, ROMs or EPROMs. [See section 3.21
The RAM is also divided into two sections of
16 Kbytes, each of which contains eight 16K by 1 bit DRAM chips. In the model A
microcomputer, only one bank of 16K is present whilst both are present in the
model B. This RAM has to be accessed by both the processor itself and also the
CRT controller. This is done by using a form of "transparent access" in which
both the processor and the CRT controller can access the RAM at the full clock
speed by interleaving the accesses on alternate phases of the system clock. [See
section 3.3]
The display is extremely versatile, and uses
two entirely different methods depending on screen mode. Mode 7 uses Teletext
hardware which produces RGB signals by having its own character generator and
accepting data from the RAM as ASCII characters. This means that it uses very
little RAM (only 1 Kbyte), and apart from providing the addressing for the RAM,
the only thing which the CRT controller has to do is to add the cursor
information and sync signals.
In the other screen modes, the information is
stored in RAM as actual bit patterns for every character that is written to the
screen. This is expensive in terms of memory usage, (between 8K and 20K in the
different modes) but it makes it extremely versatile, especially when mixing
graphics with text. The addressing of the RAM for the different modes is
performed by the 6845 CRT controller, whilst the data is taken from the RAM and
serialised by a custom designed circuit, known as the video processor. This data
is not used directly to produce RGB information, but can be thought of as a set
of logical colour numbers which are passed to an area of high speed RAM within
the video processor referred to as the colour palette. This determines, for each
logical colour number, which combination of red, green and blue is produced, and
whether or not the colour is flashing. The video processor is also responsible
for selecting either the RGB signals coming from the Teletext chip or the
signals coming from the palette and sending them out to the RGB buffers and the
PAL encoder.
This RGB information is presented, after
buffering, on the RGB connector. To provide a UHF output, the RGB signals are
combined with the sync signals and fed into a UHF modulator. A video output is
also provided which consists of a summing of the RGB signals in such a way as to
give an appropriate grey scale. On issue 4 boards onwards, the option is given
of adding colour to the video signal in order to provide a PAL encoded video
output. [See section 3.4]
Moving on round in an anti-clockwise direction
we come to the two serial interfaces, the cassette interface and the RS423.
These facilities are both provided by a standard ACIA (Asynchronous
Communications Interface Adaptor) – the 6850, and a custom designed
circuit referred to as the serial processor. This processor contains the
programmable baud rate generators for transmit and receive which provide the
clocks for the ACIA. The ACIA itself is responsible for serialising the data,
providing the control lines for the RS423 and generating interrupts, whilst the
serial processor switches these data and control lines between the cassette and
RS423 interfaces. The serial processor also provides data separator and sinewave
synthesis circuits for the cassette recorder as well as a means of detecting the
presence of the incoming tone from the recorder. [See section
3.5]
The next section is the analogue input port
which is a four channel 12 bit converter which is discussed in more detail in
section 3.9 and the interfacing survey (see chapter 7).
In the NW corner is the Econet section which
centres around a 68B54 Advanced Data-Link Controller (ADLC). This is a
sophisticated serial communications device allowing the sending and receiving of
data at a variety of speeds between as many as 254 computers. The data transfer
is synchronised by a clock signal fed to all the computers as a differential
signal on one pair of cables, whilst the data itself uses another pair of
cables. Data is both transmitted and received on the same pair of cables, but
obviously only one computer at a time is able to "broadcast" onto the data
highway. [See section 3.12]
There are two 6522 versatile interface
adaptors (VIA) on the PCB (one on the model A), the first being used mainly for
internal control and the second for external interfacing. VIA-A is used both for
control of internal hardware and also for generating interrupts from various
devices such as the ADC and the keyboard. Of its two internal timers, the first
is used for generating regular interrupts at one centisecond intervals and the
second is used occasionally by the operating system. [See section
3.6]
Of the two ports on this VIA, PA is used to
provide a slow (1 MHz) data bus for the sound and speech chips and also for the
keyboard, whilst PB is used to provide control lines for various functions
throughout the circuit board. The sound is produced by a four-channel sound
generator chip (SN76489) whilst the speech is produced by a TMS 5220 which can
get its data either from RAM through VIA-A or from a serial ROM, the TMS 6100.
This facility for accessing serial ROMs is also used to provide an external
serial ROM facility on the keyboard. [See sections 3.7 and
3.8]
Moving down to the SW corner we have the disc
controller interface based on an 8271 floppy-disc controller. This is
responsible for sending out the command signals for a floppy disk drive, and for
reading and writing the data from and to the disk drive. [See section
3.10]
The next device is VIA-B, referred to as the
external VIA, which is used to provide interfaces for a printer and user
applications. It also has two timers which are available to the user for his
own. applications programs. [See section 3.11]
The last two sections of the circuit board are
the 1 MHz extension bus and the TUBE. These provide two different ways of
accessing various external devices. The 1 MHz bus is available for more general
use but works at the slower speed of 1 MHz, whilst the TUBE works at the full 2
MHz but is only intended for use with second processors. [See section
3.13]
3. Detailed Circuit
Description
3.1 Processor + clock circuitry + reset
circuitry
The microprocessor is a 6502A and runs at
either 1 or 2 MHz. Most processing is done at 2 MHz, including accesses to the
RAM and ROM, but the processor slows down to 1 MHz when addressing slow devices,
viz. the 1 MHz extension bus, the ADC, the two VIA’s, the 6845 CRT
controller, the ACIA, and the serial processor. Clock signals for the
microprocessor are produced by a 16 MHz crystal oscillator (IC43) in conjunction
with divider circuitry in part of the video processor (IC6) which produces 8, 4,
2 and 1 MHz signals. The 1 MHz signal coming directly from the video processor
is only used for the Teletext generator chip, whilst a D-type flip-flop (half of
IC34) divides the 2 MHz clock signal in order to produce the system 1 MHz clock
(1 MHzE). A 2 MHz signal of suitable phase is produced at the output of another
D-type (half of IC31) which remembers when a 1 MHz cycle has been requested. At
the appropriate time, as governed by the 2 MHz clock, one of the 2 MHz clock
cycles is masked off by the D-type (half of IC34) and when this happens the
D-type that remembered that a request had been made, is cleared. Depending on
the phase relationship between the 1 and 2 MHz clocks at the time of the
request, the delay on the 2 MHzE clock is different as illustrated by the
diagrams below. The following simple program will produce these conditions
alternately, so that they may be viewed with an
oscilloscope.
10 P%=&3000
20 [ SEI
30 .start
40 STA &FC00
50 STA &FC00
60 JMP start
70 ]
80 CALL &3000
Case A
REQUEST
1MHzE
2MHzE
02
REF
2MHzE
1MHzE
REQUEST
02
REF
Case B
Figure 1 2 – 1 MHz
stretching
A 555 timer circuit (IC16) provides a reset
signal both at power up and also when the BREAK key is pressed. There is also a
separate reset circuit using a CR combination from the +5 volt power supply (C10
and R20 and Dl), to provide a signal called Reset A which is fed to IC3, the
internal VIA. The idea is that although the 555 timer produces a general reset
at power up or when the BREAK key is pressed, Reset A goes low only on power up.
By interrogating the interrupt register on IC3 on the occurrence of a general
reset, the microprocessor can discover whether it was a "cold start", ie power
up, or a "warm start", if the BREAK key has been pressed when the system has
already been in use for some
time.
3.2 Memory and address
decoding
31 1/4 Kbytes of ROM are catered for in the
address map. 15 1/4 Kbytes of this are contained in the operating system (IC51).
This is in fact a 16K device but 3/4K of it is left unused and it is in this
area that the I-O device memory map is situated. Four other ROMs (ICs 52, 88,
100 and 101) are on the main circuit board. They may all be 16 Kbyte devices, in
which case any one of them may be switched into the 16 Kbyte space in the memory
map by writing to the ROM select latch (IC76). Alternatively, four 4 Kbyte ROMs
may be in these four sockets in order to fill the 16 Kbyte space assigned. In
this case, a two line to four line decoder (half of IC20) is used to select
which of the four devices is being addressed by the address lines A12 and A13.
Mixtures of these two cases are allowed for, for instance two pairs of 8 Kbyte
ROMs, one pair or the other being selected by the ROM select latch and then the
ROM to be used in each pair being selected by the 2-4 line address decoder.
Address decoding for the ROMs is by IC21 which decodes memory addresses
&8000 to &C000 and &C000 to &FFFF. Locations from 0 –
&7FFF are assigned to the dynamic RAM, and this is decoded by feeding A15
into pin 4 of IC21. All the rest of the hardware is mapped within locations
&FC00 to &FEFF. This is decoded by IC22, whilst ICs 20 and 25 are used
to mask off the ROM over this range of addresses. ICs 24 and 26 decode the
individual devices within this range, some of which are read or write only. IC23
detects when a slow l MHz device is being addressed and it calls for the 6502 to
execute a slow clock cycle.
Note that in early versions of the BBC
Microcomputer, the operating system was contained within 4 EPROMs in IC
positions 52, 88, 100 and 101 while the BASIC interpreter was located in IC51.
This arrangement is abnormal and has been phased out. Refer to the link
selection survey (5.1) for more detailed information on
this.
FEE0
FEC0
FEB0
FEA0
FE60
FE20
FE50
FE40
FE00
FE08
FE10
FE1B
VDU
screens
-1900
-0E00
Start of user RAM in Model B with
disc
Start of user RAM in Model
A
TUBE
|
ADC
|
ADLC
|
FDC
|
VIAB
|
VIAA
|
---
|
ROMSEL
|
INTON
|
VIDPROC
|
INTOFF/ STATID
|
|
SERPROC
|
ACIA
|
CRTC
|
Figure 2 Memory map, including internal
hardware
3.3 CRT controller +
video processor + Teletext hardware
Random Access Memory on the Microcomputer is
provided by either 8 or 16 dynamic memory devices (ICs 53-68). These devices
store 16K bits each and therefore in the Model B, the data inputs and outputs of
one pair of devices are paralleled for each of the 8 data bits, D0 to D7. To
address 16K bits requires 14 address lines, and this is achieved on the 4816 by
having 7 inputs and latching in the addresses in two halves by using a row
address strobe (RAS) and a column address strobe (CAS). Two octal buffers
(81LS95) have to be used to multiplex the appropriate processor address lines
onto the RAM address lines. (ICs 12 and 13). However, the 6845 CRT controller
(IC2) also needs to access the RAM, and what is more, it accesses it differently
depending on whether it is working in the Teletext mode or in one of the other
graphic modes. Therefore two more pairs of octal buffers are used, ICs10 and 11
for the Teletext mode, and ICs 8 and 9 for the other modes, the main difference
being that in these modes the three least significant address bits are produced
by the character row address lines from the CRTC in order to give the
bit-mapping of the characters in the RAM memory rather than having the ROM
character generator as in the Teletext mode.
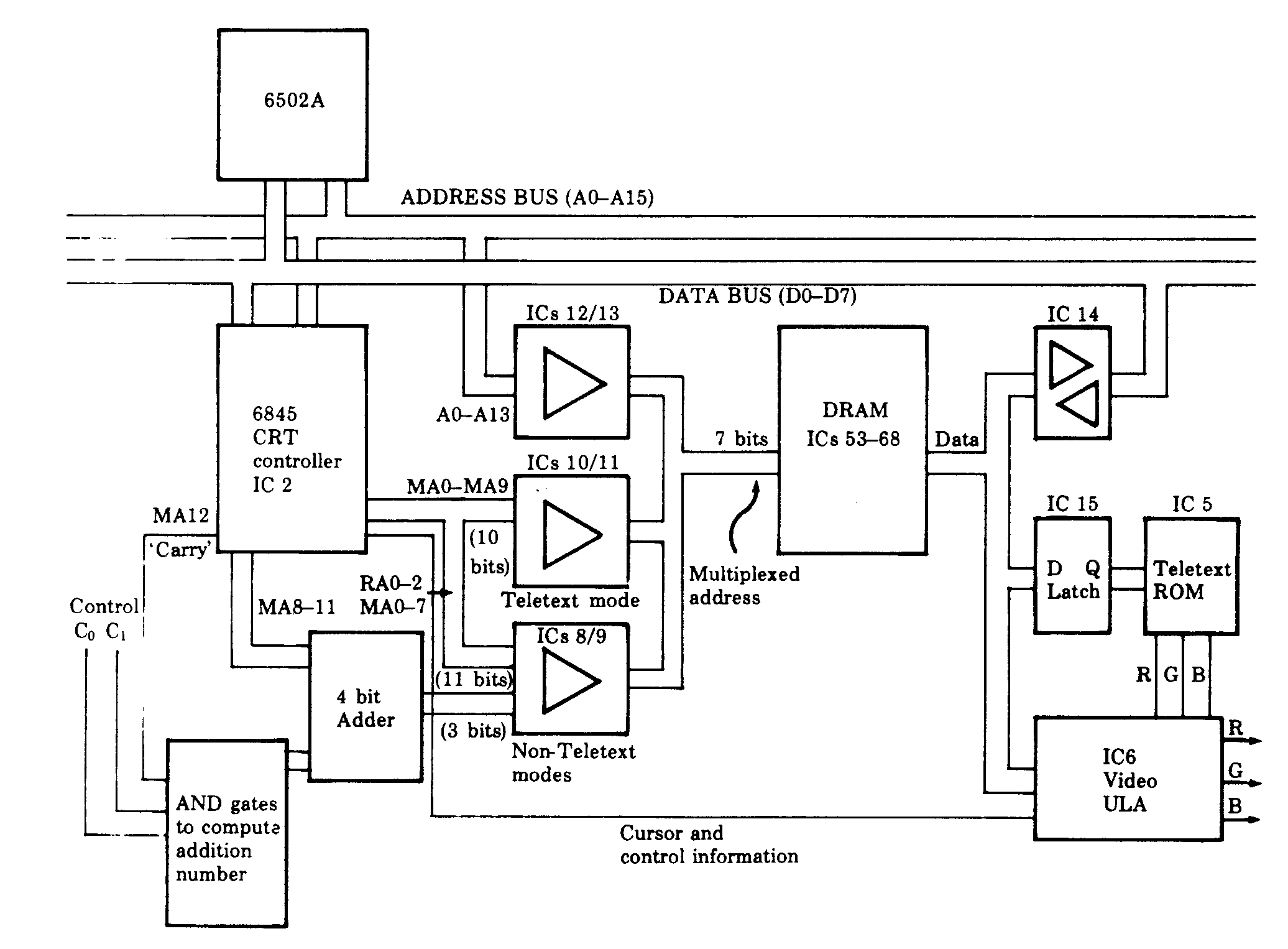
Figure 3 Block diagram of CPU, RAM and CRT
controller
The 6502 microprocessor runs from a constant
clock and so its requirements for memory access are predictable. Every 250
nanoseconds, control of the RAM address lines is switched between the
microprocessor and the CRTC. Thus, in each one microsecond period, the
microprocessor has two RAM accesses and the CRTC has two RAM accesses. Because
the CRTC generates a sequence of addresses in order to refresh the VDU display,
all the row address lines of the RAMs are constantly cycled. The addressing
methods have been designed so that in each screen mode the dynamic RAMs are
automatically refreshed by virtue of the sequential CRTC
accesses.
Figure 4 DRAM
operation
The row address strobe signal is produced by a
D-type flip-flop connected to the 8 and 4 MHz clock signals (half of IC44). This
RAS signal then drives all of the dynamic RAMs via R106. The two banks of RAM
are enabled by virtue of having their column address strobes individually
available. In model A computers, with only one bank of RAM, CAS 1 is used. In
the model B, CAS 0 controls the lower 16K and CAS 1 the upper 16K. The second
bank of RAMs is selected by a 74LS51 circuit (half of IC28) which controls the
74S139 (half of IC45) producing the CAS signals. When A14 is high the B input is
low thus selecting CAS 1. The other half of IC45 is used to select between the
processor and CRT address lines.
Using this technique, two bytes of information
are available per microsecond for refreshing the raster scanned video display.
With each horizontal line having a period of 64 microseconds, a 40 microseconds
active display area is usual. Thus, 640 bits (2 bytes x 8 bits x 40
microseconds) of information per horizontal line are produced from the
memory-mapped display. At the end of each 250 nanosecond CRTC access period, the
video processor (IC6) latches the byte from the RAM and, according to the
display mode in operation, serialises the byte into a single bit stream of 8
bits, or two bit streams of 4 bits or four bit streams of 2 bits. In this
way, display modes varying from 640 pixels in 2 logical colours to 160 pixels in
16 logical colours can be produced.
Figure 5 Colour palette
operation
The video processor contains a piece of high
speed (16MHz) static RAM called a palette. This memory can be programmed to
define the relationship between the logical colour number produced by the RAM
and the physical colour which will appear on the display. Note that the
information in the main RAM is unchanged by changing the palette; it is its
interpretation into physical colours which changes. Modes 0 to 6 in the
Microcomputer use software generated characters, that is to say, the character
font to be produced on the screen is held in the memory-mapped display area of
the RAM so that graphics and/or characters may be held. The definition of these
characters is stored in the operating system ROM from C000 to
C2FF.
Figure 6 Video ULA block
diagram
The speed of printing on the screen is much
increased by the use of hardware scrolling. There is a register in the CRTC
which is used to define the start of screen address in the screen memory. Thus
in order to scroll the screen, it is only necessary to increment this register
by the number of characters per line and then write to the memory address where
the last screen data was. The number of address lines from the CRTC, used to
address the screen memory, has to be sufficient to cater for the biggest screen
(20 Kbytes). Thus 14 address lines have to be used which means that when using
the hardware scrolling technique, the picture scrolls around in 32 Kbytes.
Consider a scroll of 8 Kbytes in a 20 Kbyte screen. The original start of screen
for the 20 Kbyte mode was &3000. After an 8 Kbyte scroll, the current start
of screen address is 65000 with the end of the screen as seen by the CRTC at
&5000 plus 20 Kbytes, which comes to &9FFF, as illustated
below.
&7FFF
Screen
RAM
&3000
&5000
&4FFF
Straight wrap around in 32K
Top of screen
&3000
&0000
&1FFF
HIMEM
Add &3000 if address >&7FFF
|
8k
|
Before
scrolling
|
|
After an 8k
scroll
|
Figure 7 Memory map to show addition of
CRTC addresses
Since there is only 32 Kbytes of RAM this
would mean that instead of accessing addresses &8000 to &9FFF you would
be accessing locations &0000 to &1FFF. Therefore when the address
produced by the CRTC is greater than &7FFF (ie MA12 = 1) you have to add to
the address from the CRTC, a number which will bring the actual address back up
to the area of RAM which is currently being used for the screen ie above HIMEM.
Thus for numbers greater than &7FFF you simply add the number &3000
which brings the addresses back to the range &3000 to &4FFF, as
illustrated in the diagram above. In the 20K modes you add &3000 (=12K), in
the 16K mode you add &4000 (=16K), in the 10K mode you add &5800 (=22K)
and in the 8K mode you add &6000 (=24K). This number to be added is defined
by the control lines C0 and C1 from the 74LS259 (IC32), and computed by some AND
gates with the result being added to the higher CRTC refresh address lines by a
74LS283 adder (IC39). The CRTC address line MA12 is used as a "carry" to
determine whether zero or the number computed by the AND gates is added to the
address lines. (Confusion may arise when looking at IC 9 on the circuit diagram
since it looks as if AA0 to AA2 are being buffered to A0 to A2. But if you look
at the pin numbers and compare them with the other 81LS95's you will see that
they are in fact buffered to the top three bits, A4 to A6. MA4 to MA7 are
buffered to A0 to A3.)
Display mode 7 is a Teletext mode and to
implement this an SAA 5050 (IC5) Teletext character generator Read Only Memory
is used. IC15 latches the information coming from the RAM prior to the SAA 5050.
When using this mode, only 1K of RAM is devoted to the display memory and the
characters are held within it as ASCII bytes. The SAA 5050 then translates these
bytes into a standard Teletext/Prestel format display.
A 6 MHz clock signal is required for the
Teletext character generator (IC5). This signal is produced by knocking a reset
flip-flop (two quarters of IC40) backwards and forwards from the 8 MHz and 4 MHz
clock signals. The output of this flip-flop is then itself inverted according to
the state of the 2 MHz clock signal by an exclusive OR gate (1/4 of IC38).
Glitches on this output are removed by R119 and C48 to produce the 6 MHz clock
signal at Pin 8 of IC37.
Figure 8 6MHz clock
generation
The CRTC is still used to generate the RAM
addresses even in the Teletext mode, but using only 1K means that only 10
address lines are needed hence the top four address lines on he 81LS95 (IC11)
are tied to logic 1. The Teletext mode is selected by setting the value of video
address start (registers 12 and 13 in the CRTC) so high that an extra "carry" is
generated on MA13. This is used to enable ICs 10 and 11, disable ICs 8 and 9 and
also enable the data latch (IC15).
3.4 RGB + PAL
encoder + UHF output
The red, green and blue logic signals produced
by the video processor are buffered by transistors Q4, Q5 and Q6 and fed out
together with a composite sync signal to the RGB connector (SK 3). The red,
green and blue lines are summed together by binary weighted resistors to feed Q7
which produces a 1V composite video signal suitable for feeding to monochrome
monitors, on which the different colours will appear as different shades of
grey. Also available from the main printed circuit board, is a UHF TV signal on
channel 36, suitable for feeding to the aerial input of a domestic television.
This output is modulated using a UM1233 for PAL. Colour is provided for domestic
televisions by a PAL (phase alternating line) encoder circuit which modulates
the colour information on to the colour subcarrier frequency. Q10 is a 17.73 MHz
oscillator circuit which is divided by a ring counter (IC46) giving 2 outputs at
the colour subcarrier frequency of 4.433618 MHz. One of these two outputs is
switched by the horizontal line frequency in order to produce the alternate
phase on each TV line. Thus on IC46 pin 9, we have the 'U' signal and on IC48
pin 11, the '+/- V' signal. A row of exclusive OR gates is used to select
different phases of the 'U' and 'V' signals according to whether a red, green,
blue, cyan, magenta or yellow colour is to be produced. These signals then drive
resistors via a row of NAND gates in order to produce the colour subcarrier
signal which is added to the luminance output from Q8 by the buffer Q9. In order
for the receiving television to interpret the colour information, a reference
colour burst has to be provided at the beginning of each line. A burst gate
pulse of approximately 5uS immediately after the horizontal sync pulse for each
line is produced at pin 4 of IC41, and it is timed by C45 and R109. This burst
gate allows through a standard colour subcarrier signal which the television
uses as its reference for the rest of that line. The PAL signal may be added to
the 1V video connector with the addition of a 470 pF capacitor between the
emitter of Q9 and the base of Q7. This is provided as a link selectable option
on later issues of the PCB (issue 4 on). In modulated PAL, diodes D20, 21 and 22
increase the luminance of the darker colours, eg blue, in order to make coloured
text displays more readable.
3.5 Cassette + RS423 + serial
processor
For both the cassette and RS423 interfaces, a
6850 asynchronous communications interface adaptor (ACIA) (IC4) is used to
buffer and serialise or deserialise the data. The serial processor (IC7),
specifically designed for the BBC Microcomputer, contains two programmable baud
rate generators, a cassette data/clock separator, switching to select either
RS423 or cassette operations and also a circuit to synthesise a sinewave to be
fed out to the cassette recorder. IC42 divides the 16 MHz clock signal by 13
(1.23 MHz) and this signal is divided further (by l024) within the serial
processor to produce the 1200 Hz cassette signal. Automatic motor control of an
audio cassette recorder is achieved by using a small relay driven by a
transistor (Q3) from the serial processor. The signal coming from the cassette
recorder is buffered, filtered and shaped by a three stage amplifier (IC35). The
RS423 data in and data out signals and the request to send output (RTS) and
clear to send input (CTS) signals are interfaced by ICs 74 and 75 which
translate between TTL and standard RB423/232 signal levels (+5V and -5V). The
control register, which is memory-mapped at &FE10, specifies the frequencies
for the transmit clock (bits 0-2) and the receive clock (bits 3-5) used by the
6850 (IC4). The switching between the cassette and RS423 inputs and
outputs
is also determined by the control register
(bit 6), and so is the motor control (bit7). R75 and C28 provide the necessary
timing elements for delay between receiving the high tone run-in signal and
asserting the data carrier detect signal to the ACIA. The value of resistor
needed is affected by the output impedance of that pin on the serial processor
which has been subject to a certain amount of variation. Thus the value of R75
has changed through the evolution of the circuit.
Figure 9 Serial ULA block
diagram
3.6 Internal
VIA
One 6522 VIA device (IC9) is devoted to
internal system operation. Port B drives an addressable latch (IC32) which is
used to provide read and write strobe signals for the speech interface, the
keyboard and the sound generator chip. Also coming from this latch are control
lines C0 and C1 which provide the memory address addition for the CRT controller
depending on the amount of RAM devoted to the display memory. Pins 6 and 7 of
the addressable latch drive the capitals lock and shift lock LEDs on the
keyboard. The rest of Port B on the internal system VIA is used to input the two
"fire button" signals from the analogue to digital convertor interface and two
response lines from the speech interface. Each time the system VIA is written
to, any changes on Port B which should affect the addressable latch are strobed
into it by a flip-flop (IC31) which is triggered from the 1 MHz clock signal.
Port A of this VIA is a slow data bus which connects to the keyboard, the speech
system chip and the sound
generator.
3.7 Keyboard
The keyboard circuit (Section 9.5) connects
via PL 13. A 1 MHz clock signal is fed to a 74LS163 binary counter, the outputs
of which are decoded by a 7445 decoder driver circuit. These outputs drive the
rows of the keyboard matrix, each row being driven in turn. If any key is
depressed, the 74LS30 gate will produce an output when that row is strobed and
this will interrupt the computer through line CA 2 of IC3. On this interrupt,
the computer will enter the key reading software. In order to discover which key
was pressed, the microprocessor loads directly into the 74LS163 the address of
each key matrix row allowing it to interrogate each row in turn. Also, the
microprocessor loads into a 74LS251 data selector, the address of each specific
key on that row. ie column addresses. In this way, the microprocessor can
interrogate each individual key in turn until it discovers which one was
depressed and causing the interrupt. Once read, the keyboard assumes its free
running mode.
3.8 Sound + speech + serial ROM
interfaces
The speech system device used is a TMS 5220
(IC99) which, on instructions from the Microprocessor, will either produce at
its audio output speech from its associated memory (IC98) or from
speech data fed to it directly from
the Microcomputer's memory. On later issue boards a variable resistor is
provided (VR 2) to adjust the clock frequency to give the best effect of the
speech. IC18 is a four channel sound generator chip which may be programmed to
give varying frequency and varying attenuation on each channel. The audio output
of the speech system device is filtered by an operational amplifier circuit with
a cut-off frequency of 7 kHz. This signal is then added to an amplified and
level shifted signal from the sound generator by a virtual earth amplifier to
which is also added an extra analogue input from the 1 MHz extension bus. This
summated audio signal is then finally filtered by an 8 kHz low pass filter. All
of these operations are done by a quad operational amplifier (IC17). IC19
provides audio power amplification to drive a speaker from PL15. A low level
audio output is provided from PL16 for feeding the auxiliary input of an
external power amplifier.
3.9 A to D
convertors
A four channel analogue to digital convertor
facility is provided by IC73. This device connects straight to the
Microcomputer's data bus and is a dual slope convertor with its voltage
reference being provided by the three diodes, D6, D7 and D8. Each time a
conversion is completed, the microprocessor is interrupted through CB1 of the
internal VIA which responds by reading the value and storing it in a memory
location.
3.10 Disc interface
IC78 is a floppy disc controller circuit which
is used to interface to one or two, single or double sided 5 1/4 inch floppy
disc drives. Logic signals from the controller to the disc drive are buffered by
two open collector driver packages IC79 and 80. The incoming signal from the
disc drive is first conditioned by monostable IC87 producing a pulse train with
each pulse of fixed width. These pulses are then fed to the data separation
circuits ICs 81 and 82. These form a digital monostable. IC86 divides the 8 MHz
clock signal down to 31.25 kHz. ICs 83, 84 and 85 are then used to detect index
pulses coming in from the drive which show that the drive is ready for a read or
write operation.
3.11 Printer + user port
interfaces
IC69 is a versatile interface adaptor. Port A
is used to provide a centronics standard parallel printer interface, with an
octal buffer, IC70, to improve on the current driving capabilities of the data
lines. Control line CA2 is used as the strobe line having been buffered by part
of IC27 and Q11. It is asserted low for approximately 5uS to signal that the
data is ready. This circuit has been changed on the various issues of the PCB as
explained in section 4.4.
Port B is left uncommitted and is free for
user applications as either input or output. For full details of what can be
done with the user port you should refer to the 6522 data sheet, but basically,
apart from being used as a straightforward input/output port, PB7 can be used as
a programmable pulse output using one of the timers, PB6 can be used as an input
to the other timer for pulse counting, and CB1 and CB2 can be used for automatic
hand-shaking and in conjunction with the VIA's own shift
register.
3.12
Econet
ICs 89 to 96 are concerned with the Econet
interface. IC89 is an Advanced Data Link Controller Circuit, type 6854 which
handles the Econet protocol. Data to be transmitted on to the network is fed
from the ADLC to the line drive circuit (IC93) via an inverting Schmitt trigger
circuit (part of IC91). Transmit data then goes through the line driver circuit
which produces a differential signal drive to the Econet cables. Received data
is detected and converted to a logic signal by one half of IC94 which is a dual
comparator circuit, type LM319. The received data is then fed back to the data
link controller circuit.
An Econet installation has a single master
clock station which provides the clock for the whole of the network. This clock
signal is transmitted around the network as a second differential line signal
and it is used to clock the data in and out of the data link controller
circuits. The network clock is detected using the other half of IC94, and the
detected clock signal is then fed to both receive clock and transmit clock
inputs on the 6854. In the presence of a network clock, the monostable circuit
(IC87) is permanently triggered and thus providing a data carrier detect signal
for the data link controller chip. Once the network clock is removed, the
monostable immediately drops out and the data carrier is no longer
detected.
The Econet is a broadcast system on which a
number of stations may attempt to transmit their data over the network at any
given time. In this case, a situation called a collision can occur and then the
transmitting stations should detect the collision and back off before trying
again to transmit over the network. Collision arbitration software is included
in the Econet system and is based on the station ID number. Collisions on the
network data lines result in the differential signal on the two data wires being
reduced and this condition is detected by IC95 which is another dual comparator
circuit. When there is a good differential data signal on the network one output
of IC95 or the other will be low, in which case the output of IC91 pin 6 will be
high, indicating no collision. When there are no collisions on the network, and
the network clock is detected by the clock monostable, the data link controller
is clear to send data over the network. When there is a collision on the network
both outputs of IC95 will go high and the clear to send condition will cease.
Note that when the computer is not connected to the network a collision-like
situation results, in which case again the data link controller will not get a
clear to send condition.
Up to 254 stations may be connected to each
Econet with each station being identified by a unique station identification
number. This station ID is programmed on the links S11 and the ID can then be
read by the octal buffer IC96. The data link controller circuit produces
interrupts which are fed to the processor's NMI line. These interrupts can be
enabled and disabled under software control by using the address-decoded
signals, INTOFF which is achieved by reading the station ID at &FE18, and
INTON which is generated by reading &FE20. (Writing &FE20 loads the
Video processor register.)
3.13 1 MHz
bus
The address and data lines, A0 – A7 and
D0 – D7, together with two page select lines are available as the 1 MHz
extension bus to which various peripheral devices may be connected, eg Teletext
interface. All accesses to this bus will be at a 1 MHz processor speed, although
links are provided to increase this to 2 MHz if desired (see the selection link
survey). The octal buffer (IC71) and the octal transceiver (IC72) are used to
interface these signals to the internal data and address buses, IC72 being
enabled only when either "FRED" or "JIM" is accessed (pages &FC00 and
&FD00).
3.14 Power supply
The power supply unit produces 5 volts at 3.75
amps and -5 volts at 100 milliamps for use on the main circuit board. Some
auxiliary power for accessories is also available on an external connector and
this includes +12 volts at 1.25 amps, but the amount of power available depends
on what hardware is connected internally – Econet, disc interface,
sideways ROMs etc.
The power supply connects to the main circuit
board by seven push-on connectors with the +5 volts being fed to three different
points across the main circuit board. These points are all connected together
electrically. However, by distributing the power in this way the need for very
large copper tracks to distribute power around the board is avoided. Most
computers in production will have a switched-mode power supply, the circuit
diagram for which is given. However it is not recommended that attempts should
be made to repair this power supply, instead it should be treated as a module to
be exchanged. This is because of the stringent safety regulations relating to
such units. A small number of early computers have a linear power supply unit
with a conventional mains transformer and regulator circuit. These also should
be treated as modules to be exchanged rather than serviced, though it should be
noted that the three outputs are from separate regulators, thus it is possible
for power to appear say on two out of the three pairs of
connectors.
View from rear of free plug
+5V Earth
0
(Orange)
+12V Earth
0 (Red)
+5V
0(Yellow)
+12V
0(Brown)
NC
0
-5V
0(No cable)
Supplies:
+5V @ 1.25A
+12V @
1.25A
-5V @
75mA
Mating connector is AMP
housing 1-350234-9
+ male
pins 350-664-1
Figure 10 BBC auxiliary PSU
outputs
4 Upgrading the
PCB
In these instructions about how to add extra
hardware to the PCB for disc, Econet, speech etc, some differences may occur
depending on which hardware is already fitted. This is made clear within each
set of instructions. In order to locate the positions of various of the
selection links, reference should be made to section 5.2 which gives the X-Y
coordinates of each link. Dealers and service centres performing these upgrades
must also conform to upgrade procedures and requirements as notified by their
supplier, and should refer to any available information updates for latest
details.
4.1 Modification A
Convert from EPROM MOS to ROM
MOS
i) Remove the four MOS EPROMs from their
sockets IC52, IC88, IC100 and IC101.
ii) Remove the BASIC ROM from the IC51 socket
and replace it in the IC52 socket.
iii) Insert the MOS ROM into the IC51
socket.
iv) Set the following link positions using
MOLEX jumpers (if fitted or, tinned copper wire):–
S18 – North
S19 – East
S20 – North
S21 – 2 x
East/West
S22 – North
S32 – West
S33 – West
v) Test using a FIT and, if available, a PET
(see section 6.2).
4.2 Modification B
Convert Model A to Model
B
i) The following parts are
required:–
8 off 4816AP-3 IC61 to
68
1 off 6522 IC69
2 off 74LS244 IC70, 71
1 off 74LS245 IC72
1 off uPD7002 IC73
1 off 88LS120 IC74
1 off DS3691 IC75
1 off 74LS163 IC76
1 off 74LS00 IC77
1 off 6-pin DIN socket MAB6H
SK3
1 off 5-pin DIN socket MAB5WH
SK4
1 off 15-way D-type socket 164801-1
SK6
2 off 34-way header 3431-1302 PL8,
PL11
1 off 26-way header 3429-1302
PL9
1 off 20-way header 3428-1302
PL10
1 off 40-way header 3432-1302
PL12
ii) Insert the above ICs into the sockets
provided on the main circuit board. Solder the connectors on to the printed
circuit board.
iii) Cut the wire links at link positions S12
and S13. Move the MOLEX link at position S25 from South to
North.
iv) On issue 1, 2 or 3 circuit boards only,
add a 2k2 ohm resistor between PL9 pin 1 and +5v on the solder side of the
circuit board using a resistor with sleeved leads. +5v is available at IC85, pin
16 (33 mm due North of pin 1).
v) On issue 1, 2 or 3 circuit boards only, cut
the track connected to PL9 pin 23 (this may have previously been cut), then link
IC69 pin 40 to PL9 pin 19. This modification may have been made, and, if so, a
check should be made to ensure that it has been correctly
performed.
vi) On issue 1 and 2 circuit boards only, PL9
pin 26 should be cut out of the header. Care should be taken to ensure that the
pin is cut right back so that no connection can be made to
it.
vii) On issue 1 and 2 circuit boards only, a
BC239 transistor should be added in place of link S1 as follows:– Cut the
track between the centre and South pins of S1 on the solder side of the circuit
board. Cut the two tracks connected to the North pin of S1 on the solder side of
the circuit board, then reconnect the ends of these tracks leaving the North pin
isolated. Insert a BC239 transistor into the S1 position with the base in the
South pin, the emitter in the North pin, and the collector in the centre pin.
Finally, link the North pin of S1 to IC27 pin 7 with a short length of insulated
wire.
viii) On issue 1 or 2 circuit boards only, add
a 4k7 ohm resistor (R162) between the existing two holes located approximately 5
mm East of IC70 pins 11 and 13, as shown below.
R162
4k7
IC70
Figure 1 1 Adding R162 on issues 1 and 2 of
PCB
ix) On issue 1 circuit boards only, disconnect
the LPSTB signal between IC69 pin 18 and PL10 pin 2 by cutting the track on the
solder side of the circuit board which is connected to IC69 pin
18.
x) Test using a FIT and, if available, a
PET.
4.3 Modification C
Add Speech Option
i) The following components are
required:–
1 off Integrated Circuit TMS6100
IC98
1 off Integrated Circuit
TMS5220 TC99
ii) On issues 2 and 3, the following
modifications are needed.
On the component side of the main
PCB:
– Cut the track between IC3 pin 16 and
the through-hole 8mm to the
west.
– Cut the track between
IC3 pin 17 and the through-hole 10mm to the west.
On the solder side of the
PCB:
– Link the through-hole 10mm to the west
of IC3 pin 17 to IC3 pin 16
–
Link the through-hole 8mm to the west of IC3 pin 16 to IC3 pin
17.
(These operations switch the signal lines to
IC3 pins 16 and 17.)
Then, also on the solder side of the
PCB:
– Cut the track between IC98 pins 13 and
14.
– Link IC98 pin 13 to PL14
pin 3 (0 volts).
iii) Issue 1 keyboard PCBs also need modifying
as follows:–
On the solder side of the PCB, cut the track
between pins 14 and 15 of the edgecard connector. The pins are those furthest
from the speaker. (ie further east).
On the solder side of the PCB, link pin 14 of
the edgecard connector to 0 volts. This can be found on either of the capacitor
legs nearer the centre of the PCB.
iv) When the modifications are complete,
procede as follows:–
Reconnect the keyboard to the main PCB. Add
the new connector for PL14, then, with the computer turned off, test for
continuity between the following points:
Edge connector pin number
6
|
7
|
8
|
9
|
10
|
11
|
12
|
13
|
14
|
15
|
1
|
3
|
4
|
5
|
6
|
7
|
10
|
11
|
13
|
14
|
IC98 pin number
Note: On the edge connector, pin 1 is nearest
the speaker, thus the polarising key is pin 3 and pins 4 and 5 are
"empty".
Also check that there are no short-circuits
between any of the edge connector pins. Repeat the tests for the other edge
connector.
v) Insert ICs 98 and 99, turn the machine on
and type:
REPEAT SOUND-1,GET,0,0:UNTIL0
<RETURN>
Now press any alphanumeric key and you should
hear the voice synthesis operating. If the pitch is wrong, follow the
instructions in vi) below.
If there is no speech, double check the
modifications and try again.
vi) The pitch of the speech must be set. From
Issue 4 PCBs onwards this is a simple matter of adjusting VR2 which is situated
just west of IC98. On Issue 1, 2 and 3 PCBs, the resistor R32 (between ICs 98
and 99) may need to be changed to achieve the best result. The method for
setting the pitch is to connect a frequency meter to pin 3 of IC99 and to adjust
VR2 until the mater reads 160 kHz (+ or – 100 Hz), or as close as is
obtainable by changing R32.
vii) Reassemble the machine. Before fitting
the ROM socket cover into the case lid, remove the perforated section of the
black label above the ROM sockets. It may be necessary to trim the label to
match the case cutout. For early version cases (without a rib on the underside
behind the keyboard cutout), remove the two small lugs on the ROM socket cover
before fitting.
viii) Test using a FIT and, if available, a
PET.
4.4 Modification D
Add 5 1/4 inch Disc Interface to Basic Model
B
i) The following parts are
required:–
1 off 8271 IC78
2 off 7438 ICs 79,80
1 off 74LS10 IC82
2 off 74LS393 ICs 81,86
2 off CD4013B ICs 83,84
1 off CD4020B IC85
1 off 74LS123 IC87 (Not required if Econet
already fitted)
1 off 2764 EPROM (DFS) IC88 (or IC100 if
Econet fitted; but not required if DNFS already fitted)
ii) Insert the ICs listed above into the
sockets provided on the main circuit board.
iii) On issue 1 or 2 circuit boards only,
connect the two pads of link position S8 with a wire link.
iv) If the MOS ROM version 0.1 is fitted in
position IC51 then it must be replaced by a 1.2 MOS, see modification
A.
v) If the existing power supply does not
incorporate an auxiliary power output socket it must be exchanged for a suitable
unit (eg ASTEC type).
vi) On issue 1, 2 or 3 circuit boards only,
cut the leg of IC27 pin 9 as close to the PCB as possible and the track
connected to it on the component side of the circuit board between IC27 and
IC89, then reconnect the cut IC leg to the East pad of link S9 with a short
length of insulated wire.
vii) On issue 4 boards onwards, cut the TCW
link at position S9.
viii) Set the following link positions using
MOLEX jumpers:–
S18-North
S19-East
S20-North
S21-2 x East/West
S22-North
S32-West
S33-West
ix) Test using a FIT and, if available, a
PET.
4.5 Modification E
Add Econet Interface to Model
A
i) The following parts are required:
–
5 off 14-pin DIL IC
sockets
1 off 20-pin DIL IC
sockets
1 off 28-pin DIL IC
sockets
1 off 74LS163 IC76 (already fitted on model
B)
1 off 74LS123 IC87 (Not required if disc
already fitted)
1 off 68B54 IC89
1 off 74LS132 IC91
1 off 75159 IC93
2 off LM319 ICs 94,95
1 off 74LS244 IC96
1 off 74LS74 IC97
1 off 10uF Tantalum Capacitor
C18
1 off 10uF Ceramic Capacitor
C23
1 off 5-pin 180 degree DIN socket
SK7
1 off SX22K SIL resistor pack
RP2
1 off 2764 EPROM with NFS IC88 (not required
if DNFS already fitted)
2 off Rows of 8 MOLEX pins
S11
20 off 2% tolerance 1/4W resistors as
follows:–
R34-10k R40-100k R48-1k
R62-56k
R35-l0k R41-l00k R51-l0k
R63-56k
R64-1M5 R44-1M5 R52-1k0
R36-1M5 R45-l0k R59-56k
R38-look R46-1k0 R60-56k
R39-l00k R47-1k5 R61-1k0
ii) Solder all of the above passive components
onto the main PCB.
iii) Insert all of the above integrated
circuits into their sockets.
iv) Cut the wire links at link positions S2,
S12 and S13. (S12 and S13 should already have been cut on Model
B's)
v) Set the following link positions using
MOLEX jumpers:–
S18-North
S19-East
S20-North
S21-2 x East/West
S22-North
S32-West
S33-West
vi) On issue l, 2 or 3 boards only, the
following modifications are required:
Remove the capacitor C17 and replace it with a
2.2nF capacitor. Cut the PCB track from IC26 pin 6 to IC96 pins 1 and 19 leaving
the track from IC26 pin 6 to IC97 pin 2 intact. Cut the track from IC89 pin 26
to IC97 pin 4 and link IC26 pin 9 to IC96 pins 1 and 19 and also to IC97 pin
4.
vii) Test using a FIT and, if available, a
PET.
4.6 Modification F
Add 8 inch disc interface to Model
B
(As Modification D – Add 5 1/4 inch disc
interface, but add....)
x) Set the following link positions by cutting
the indicated PCB track and inserting a wire link.
LINK
|
CUT TRACK
|
WIRE LINK
|
S4
|
East (Solder side)
|
West
|
S10
|
West (Component side)
|
East
|
S27
|
West (Solder side)
|
East
|
4.7 Partial upgrading
If you want to upgrade a Model A to enable it
to run software intended for use with a model B, but do not want all the various
interfacing facilities, then it is only really necessary to add the RAM and the
6522 VIA and change link S25. The VIA is needed as some professional software
uses its hardware timers.
If you want to use sideways ROMs then you will
need to add the 74LS163 (IC76) and be sure that links Sl2 and S13 are
cut.
5 Selection links
and circuit changes
5.1 Selection Link Survey
Here is a survey of the options which may be
selected on the Microcomputer by selection links S1 to S39. These links may take
the form of tracks on the circuit board which can be cut, soldered wire links,
or shorting jumpers, plugging on to the rows of pins. This is followed by a
tabular survey of the options selected in production on a standard model B
Microcomputer.
Option Select Links are as
follows:–
1. Used only on issue 4 and succeeding boards
to select printer strobe or direct output from CA2.
2. OPEN enables ECONET
NMI
CLOSED disables ECONET
NMI
– Do not fit this link with IC91 in
place.
3. Clock base frequency selection for
ECONET
– Not used after issue
3.
4. EAST selects 5 1/4"
disc
WEST selects 8"
disc.
– This changes the pin connection of the
"side select" line on the disc interface.
5. NORTH enables ECONET
clock
SOUTH disables ECONET
clock.
– Not used after issue
3.
6. NORTH divides ECONET clock by
2
SOUTH divides ECONET clock by
4.
– Not used after issue
3.
7. WEST applies +5v to pin 30 of disc
controller (IC78).
EAST applies 0v
to pin 30 of disc controller.
– Readable by software, bit 0 of the
result register of the 8271. Not used.
8. CLOSED links disc head load signal to
PLS.
OPEN isolates disc head load
signal from PLS.
9. CLOSED disables DISC
NMI.
OPEN enables DISC
NMI.
Do not fit IC78 with this link closed. Due to
PCB faults, various different modifications are necessary with different issue
boards in order to use the disc interface. (See section 4, modification
D.)
10. WEST selects 5 1/4"
disc.
EAST selects 8"
disc.
- Changes the pin connection of the "index"
line on the disc interface.
11. Selects Econet station ID. (NORTH is
LSB)
– See Econet upgrade instructions
– section 4, modification E.
12. CLOSED ties ROM select line A to
0V.
OPEN ROM select line A driven by
IC76.
– On model A's, IC76 is not fitted
because sideways ROM'S are not used. ROM 0 (IC52) is permanently selected. Do
not fit IC76 with this link closed.
13. CLOSED ties ROM select line B to 0V at
IC20.
OPEN ROM select line B driven
by IC76.
– Do not fit IC76 with this link closed.
See comments on link 12.
14. CLOSED disables ROM output from page FD,
enables JIM.
OPEN enables ROM output
from page FD, disables JIM.
– If link 14 is open then link 15 must
be closed and R72 must be fitted. The purpose of this link was to provide access
to an extra page of the OS ROM for development purposes. It is unlikely to be
used in production machines as it disables the 1MHz bus.
15. CLOSED disables fast access to page FD via
IC23.
OPEN enables fast access to
page FD via IC23.
– Link 15 must be closed if link 14 is
open and R72 must be fitted. See comments on link 14.
16. CLOSED disables fast access to page FC via
IC23.
OPEN enables fast access to
page FC via IC23.
– Link 16 must be closed if link 17 is
open and R73 must be fitted. See comments on link 14.
17. CLOSED disables ROM output from page FC,
enables FRED.
OPEN enables ROM
output from page FC, disables FRED.
– If link 17 is open then link 16 must
be closed and R73 must be fitted. See comments on link 14.
18. SOUTH forces slow access to IC100
ROM.
NORTH allows fast access to
IC100 ROM.
– To allow the use of 1MHz
EPROMs.
19. WEST forces slow access to ROMs IC52, IC88
and IC101.
EAST allows fast access
to ROMs IC52, IC88 and IC101.
-Diodes D10, D11 and D12 may be selectively
added to slow down ROMs IC101, IC88 and IC52 respectively when link 19 is in
WEST position, but for any ICs to have slow access, R55 must be
added.
D10, 11 a 12 and R55 are not fitted from issue
7 onwards.
20. SOUTH connects high ROM select bit to IC20
decoder from A 13.
NORTH connects
high ROM select bit to IC20 decoder from ROMSEL l.
21. 2 x NORTH/SOUTH selects blocks 8 to B in
IC51 and blocks C to F in ICs 52, 88, 100, and 101. (4 EPROMs for
OS)
2 x EAST/WEST selects blocks C to F in IC51
and blocks 8 to B in ICs 52, 88, 100 and 101. (OS in IC51)
22. SOUTH connects low ROM select bit to IC20
decoder from A 12.
NORTH connects
low ROM select bit to IC20 decoder from ROMSEL 0.
23. OPEN RS 423 receiver not terminated
(DATA).
CLOSED RS 423 receiver
terminated (DATA).
24. OPEN RS 423 receiver not terminated
(CTS).
CLOSED RS 423 receiver
terminated (CTS).
25. SOUTH selects CAS 1 only, for 16K RAM
configuration.
NORTH selects CAS 0
and 1 for 32K RAM configuration.
– If removed altogether, this selects
CAS 0 only, but this should only be used for testing purposes on a Model
B.
26. WEST selects normal video
output.
EAST selects inverted video
output.
27. WEST selects 8 MHz clock for 5 1/4"
disc.
EAST selects 16 MHz clock for
8" disc.
28. WEST selects base baud rate. (1200
baud)
EAST selects 1300 baud
cassette rate.
– If link 28 EAST position RS 423 baud
rate is also changed by the same factor:– 13/12.
29. EAST selects base baud rate. (1200
baud)
WEST selects 1300 baud
cassette rate.
– If link 28 is in the WEST position, RS
423 baud rates are also affected.
30. increase the flexibility used for the
addition of extra sideways ROM sockets. This would be in connecton with other
links (S20,21,22) to enable a total of 16 sideways ROMS to be
selected.
31. WEST selects +ve CSYNC to RGB video
output.
EAST selects -ve CSYNC to
RGB video output.
32. WEST selects A 13 input to pin 26 of ROMs
IC52 and IC88.
EAST selects +5v
input to pin 26 of ROMs IC52 and IC88.
– This enables 24 pin ROMs to be used in
the 28 pin socket.
33. WEST selects A 13 input to pin 26 of ROMs
IC100 and IC101. EAST selects +5v input to pin 26 of ROMs IC100 and
IC101.
– This enables 24 pin ROMs to be used in
the 28 pin socket.
34-38. These are used to provide contact with
the ROM decoder (IC20) and the chip select lines of ROMs 52, 88, 100 and 101, in
order to allow the use of extra ROM sockets on an external PCB. (Implemented
from issue 4.)
39. CLOSED adds colour burst signal to the
black and white video signal to produce PAL encoded video on the BNC
socket.
OPEN Black and white video on BNC socket.
(Implemented from issue 4.)
5.2 Table of link
options.
The following table gives a list of selection
links showing their positions on the circuit board (mm E,N from SW corner) and
on the circuit diagram (grid reference, see main PCB circuit diagram). The links
made in production on a standard model B without disc or Econet interfaces are
also given.
P = plugable link, T = track, W = wire link, C
= closed, O = open.
N S E and W refer to orientation of tracks or
plugs.
Some links have been omitted on later issue
boards, whilst others have been added.
LINK
|
PCB
|
Circuit
|
Options
|
|
position
|
diagram
|
(Model
B)
|
1.
|
2,108
|
2,5
|
T
N (Not used on issues 2 and 3)
|
2.
|
2,161
|
12,7
|
W
C
|
3.
|
2,173
|
14,14
|
–
– (Not fitted after issue 4)
|
4.
|
12, 12
|
1,9
|
T
E
|
5.
|
26,195
|
14,9
|
–
– (Not fitted after issue 4)
|
6.
|
26,205
|
15,9
|
–
– (Not fitted after issue 4)
|
7.
|
30, 65
|
4,9
|
T
E
|
8.
|
32, 15
|
2,9
|
T
C
|
9.
|
35,128
|
3,10
|
W
C
|
10.
|
45, 15
|
1,8
|
T
W
|
11.
|
75,210
|
13,10
|
P
– (When Econet fitted)
|
12.
|
97, 70
|
9,8
|
W
O (Wire link in Model A)
|
13.
|
100, 67
|
9,8
|
W
O (Wire link in Model A)
|
14.
|
101, 53
|
7,10
|
T
C
|
15.
|
107, 97
|
7,9
|
T
C
|
16.
|
108, 90
|
7,9
|
T
C
|
17.
|
108, 52
|
7,10
|
T
C
|
18.
|
110, 52
|
708
|
P
N
|
19.
|
102,102
|
7,8
|
P
E
|
20.
|
123, 55
|
9,8
|
P
N
|
21.
|
122, 65
|
9,8
|
P
2 x EW
|
22.
|
127, 70
|
908
|
P
N
|
23.
|
177,215
|
13,3
|
W
O
|
24.
|
181,195
|
13,3
|
W
O
|
25.
|
215,185
|
7,5
|
P
N
|
26.
|
221, 68
|
10,1
|
P
W
|
27.
|
226, 95
|
1,7
|
T
W
|
28.
|
237,144
|
12,6
|
T
W
|
29.
|
237,146
|
12,6
|
T
E
|
30.
|
284, 20
|
8,8
|
–
– (For external connections)
|
31.
|
270,170
|
14,3
|
P
W
|
32.
|
295, 65
|
9,9
|
P
W
|
33.
|
295, 67
|
10,9
|
P
W
|
34.
|
200, 65
|
9,8
|
T
C (From issue 4 onwards)
|
35.
|
245, 20
|
9,8
|
T
C (From issue 4 onwards)
|
36.
|
260, 20
|
9,8
|
T
C (From issue 4 onwards)
|
37.
|
280, 20
|
9,8
|
T
C (From issue 4 onwards)
|
38.
|
300, 15
|
9,8
|
T
C (From issue 4 onwards)
|
39.
|
255,215
|
9,8
|
T
O (From issue 4 onwards)
|
5.3 Circuit
Modifications from issue 1 to issue 7.
In this next section are listed the more
important changes which have taken place in the circuit design as it has evolved
from issue 1 to issue 7. Since there are so few issue 1 boards in circulation at
the moment, we will ignore the changes from 1 to 2 and suggest that if you come
across an issue 1 board and cannot solve any fault which occurs on it, that you
should consult the Technical Services Department of Acorn Computers
Ltd.
5.3.1 Changes from issue 2 to
3.
1. The ACK line on PL9, the printer port, was
moved from pin 23 to pin 19.
2. A, 4k7 resistor (Rl62) was added to the ACK
line to pull it up to +5v.
3. Link S1 was removed in order to put in a
transistor inverter, Q11. 4. Pin 26 of PL9 was left unconnected to avoid the
problem that this pin is used on some printers as the reset
line.
(Changes 1-4 were made retrospectively on most
of the issue 1 and 2 circuit boards).
5. Various modifications were made in the
region of S9 and IC27 at various stages, and so for the correct implementation,
see section 4 on the modification for adding the disc
interface.
6. A 2k2 pull up resistor (R170) was added to
the strobe line of the printer port (pin 1 of PL9).
7. R109 became select on test (SOT) with a
value between lk8 and 2k7 in order to set the correct colour burst
length.
8. C51 also became SOT at a value between 15pF
and 22pF in order to set the colour burst frequency to the correct value of
4.4336 MHz + or – 100 Hz.
9. In order to improve the waveform of the
16MHz signal, C42 was at one stage a fixed capacitor with a trimming capacitor
in parallel. Therefore various issues of boards will have various different
values for C42. Also the gate used (IC40) was changed from a 74LS00 to a
74S00.
5.3.2 Changes from issue 3 to issue
4.
1. The Econet circuitry was modified in
various ways. The clock generator and terminator components were removed,
certain component values were changed in order to improve circuit performance
and the layout was altered in order to improve the shielding and to reduce
cross-talk.
2. A 22k resistor (R174) was introduced from
pin 20 of IC7, the serial processor, to 0 volts to ensure that if IC74 was
absent that the CTSI line was held low.
3. Having added the 2k2 pull up resistor
(R170) to printer port strobe line and put Q11 in its own position, S1 was
reinstated.
4. The circuitry associated with S14 to S17,
which change the 1MHz bus to 2MHz, on the issue 3 PCB was incorrect. This should
be checked against the current circuit diagram if it is to be
used.
5. The position of D13 was changed to put it
in parallel with the relay coil rather than across the collector and emitter of
the transistor (Q3).
6. The connections from the speech circuit
(IC99) to the VIA were changed. VSPRDY and VSPINT were changed over to connect
to PB7 and PB6 respectively.
7. A resistor (R171) was connected in series
with the EOC line of the ADC (IC73) in order to prevent momentary output
contention which may occur during power-up.
8. A 4k7 resistor (R173) was connected between
pin 7 of IC89 and +5v, as the output is open collector.
9. Resistors R104, R125, R142, R149, and R153
which were in series with the ROM chip select lines were replaced by copper
links formed on the component side of the PCB. (S34 to 38)
10. A 10k resistor (R172) was introduced
between the analogue input on the 1MHz bus and 0 volts in order to reduce the
input impedance and hence improve the signal to noise ratio. (See section
6.4)
11. Link S39 was added in order to connect the
470pF capacitor, C58 from the base of Q7 to the emitter of
Q9.
12. A 220nF capacitor (C59) was added in
series with R90 in order to AC couple the log amplifier on the cassette
interface.
13. A number of changes were made to the
Econet control lines in order to speed up software control. For details of how
to bring earlier issue boards up to the current issue, see the section on
upgrading the Econet system (section 4, modification E).
14. Provision was made for mounting a
right-angled phono socket as an alternative to the free-wired BNC socket
normally used for video output.
15. A 200k potentiometer (VR2) was added in
parallel with R32 in order to adjust the operating frequency of IC99 for the
appropriate pitch of the speech output.
16. At some stage between issues 3 and 4, C34,
the cassette output coupling capacitor was increased from 47nF to
220nF.
5.3.3 Changes from issue 4 to issue
7.
(Issues 5 and 6 never went into
production).
1. R114 changed to its present value of 18
ohms 1W, and C42 changed to 33pF.
2. R75 went to its final value of 82k. (The
reason for the change in value of R75 was to control the data carrier detect
delay time to avoid loosing the first bit of the first byte of the first block
when recording data.)
3. The diodes and resistors on the ROM select
circuitry which can be used to produce 1MHz operation were
omitted.
4. Links S18 and S19 are made with tinned
copper wire.
5. When the video processor ULA was replaced
by the first set of custom-designed ICs, a modification was necessary. S26 was
left unconnected and a wire link was made from the TTX-VDU line (pin 17 of IC2)
to the invert input of the videoprocessor (pin 27 of IC6). Later versions of the
custom IC made this modification unnecessary.
All other changes from issue 4 to issue 7 were
cosmetic changes including some thickening up of the tracks to improve the power
supply distribution.
6 Servicing and
Fault-finding
6.1 Introduction
Before starting, it should be realised that
attempt at repair by any person other than a registered dealer or service agent
will void the warranty.
6.2 Test Equipment
The very minimum test equipment required in
order to trace even the simplest fault is a digital multi-meter and an
oscilloscope (or possibly a logic probe). It is difficult in a book such as this
to do more than give a few general guide-lines as to the sort of problems to
look for, and a few techniques which might be used.
Acorn Computers Ltd supply two pieces of test
equipment which are specifically designed for the BBC Microcomputer which are
known as the PET (Progessive Establishment Tester) and the FIT (Final Inspection
Tester). Whilst the service agent or dealer might be expected to have these
pieces of equipment, the average user is unlikely to feel that it is worth
purchasing them for the limited amount of fault-finding he or she would be
likely to do. The purpose of the PET, which is the more expensive of the two
items, is to take an apparently lifeless computer and attempt to find out where
the fault lies. The FIT on the other hand is somewhat simpler and its aim is not
to isolate a known fault but to check whether an apparently working computer is
in fact working in all respects. Both the PET and the FIT are the subject of
entirely separate documents produced by Acorn Computers
PLC.
Two other very useful pieces of "test
equipment" are a can of freezer spray and a hair-dryer! It is fairly common for
faults in some of the ICs to be associated with temperature conditions.
Therefore if you have reason to suspect a particular component, it is sometimes
helpful to "exercise" the device by the use of these two items. This can
sometimes show up a fault quite clearly. However, this can be slightly
misleading in cases where the fault is caused by a timing problem on some
device. This is because changing the temperature conditions of one device which
may not itself be at fault, may, by changing the relative timing, bring the
timing back into a working condition. Therefore having discovered a device which
apparently has a temperature fault, before de-soldering it, it is well worth
temperature cycling the associated components.
6.3 Fault
Isolation
Having checked that the apparent fault is not
a problem with the program, the first thing to do is to isolate the problem to a
particular area of the computer. For example, if the problem is in loading and
saving programs with a cassette recorder then attention should be focussed on
the cassette interface itself. However, this is not as easy as it sounds in some
cases because of the links between various sections of the circuit. It would
probably be worthwhile reading through most of the circuit description given in
this book, in order to try to gain an understanding of the operation of the
computer as a whole before trying to deal with one apparently isolated section
of the computer's hardware.
The simplest fault to check for is
malfunctioning of the power supply. Voltages can be measured at the terminals on
the PCB where the power leads are attached, but it is worth checking,
particularly with the older linear type power supplies, that the +5 volts is
available on each of the three pairs of connectors. It is also worth checking
that the -5 volts is present because although the processor, memory and VDU will
all function normally if the -5 volts is not present, it is essential for
cassette, sound, speech and RS423 interfaces.
If the power supply is NOT working then you
should NOT attempt to repair it. The reason is that in order to maintain the
safety specification to which the computer was designed, any repair to the power
supply, including replacement of power supply cable, must be checked for earth
continuity at a current of not less than 10 A, and must undergo a Dielectric
Withstand Test between both live and neutral to ground of 1500 V AC. This
requires specialist equipment and training and should not even be attempted by
dealers, unless they have the necessary equipment and
expertise.
The worst kind of fault with a microprocessor
system is that the processor is unable to fetch instructions from the ROM,
process them and then produce some sort of result which the operator can see or
hear. In the case of such faults, the whole system appears completely dead and
it is very difficult to locate the specific fault. This kind of problem is made
worse on this particular computer because of the technique used to refresh the
dynamic RAM. Not only must the processor fetch instructions from ROM and process
them, but also it must successfully program the CRT controller which, in turn,
must begin to produce refresh addresses for the dynamic RAM before the system
memory can operate.
Assuming then that the machine appears totally
dead even though the power supply unit is apparently working, and that you do
not have access to a PET, then here are a number of things you could
check:–
i) Check that the reset line on the 6502A (pin
40) is high, and only goes low when BREAK is pressed.
ii) Check that the IRQ line is not permanently
in either a low or high state. (Pin 4 of the 6502A)
iii) Check for the presence of the various
clock signals, for example, the clock input and output on the 6502A (pins 37 and
3), and the 1, 2, 4 and 8 MHz signals on pins 4, 5, 6 and 7 of the video
processor (IC6).
iv) A very useful pin to check is pin 7 on the
6502A. This is the sync pin and, although it is not actually used in the
circuit, it gives an indication of whether or not the 6502A is fetching any
instructions. If this is permanently high or low then the 6502A is totally
stalled.
v) Check that the read-write line (pin 34) of
the 6502A is working normally and also check that the same signal, having been
inverted and re-inverted, is available at pin 10 of IC33.
vi) Check for the horizontal and vertical sync
signals coming from the CRTC (pins 39 and 40 of IC2) which will reveal whether
or not the CRTC has been successfully programmed at system
reset.
If you do detect something abnormal in one of
these tests then the next stage would be to remove from the board any devices in
IC sockets which are unnecessary to the basic operation of the computer. For
example, the 6850 ACIA (IC4), the serial processor (IC7), the ADC Converter
(IC73) and the external 6522 (IC69). Having removed these devices, if the fault
disappears, then it may simply be a case of replacing them one by one until the
fault reappears. If the fault remains, then if you have any spare ICs, or
another machine with which you could exchange ICs, it would be worth replacing
the internal VIA (IC3), the 6502A (IC1), the 6845 (IC2) and the video processor
(IC5).
At this stage the next thing to try is to
examine each of the individual address and data lines to see if one or more of
these lines is permanently high or low. If so, look for short circuits, solder
bridges etc on that line. It is worth checking these lines both on the 6502A
itself and also IC51, the operating system ROM.
When looking around the board at various
points with an oscilloscope, try to find any waveforms which either have "slack"
edges, ie sloping rather than square, or which have voltage levels which are not
within the normal TTL range. (Logic 1 must be greater than 2.8V and logic 0 less
than 0.8V, though normally one would not expect to see voltages of less than
about 3.4V or more than 0.4V.)
Another very useful test with a model B, is to
move link S25 to the south position to see if the computer will operate in the
16K mode, in which case, it suggests a problem with the CAS 0 area of RAM. Then
if you remove S25 altogether, it puts the machine again into the 16K mode but
this time with the CAS 0 area enabled and the CAS 1 area
inoperative.
6.4 Most Common
Faults
In the following section, we shall try to give
some ideas which have been colllected from various people who have been doing a
good deal of servicing and repair work on BBC Microcomputers. There will be no
particular order to the comments but reading through all of them should give
some useful ideas about faults which are likely to occur.
- A common reason for getting sound-on-vision
effects is that the power leads have become intermittent. To check whether they
are giving a problem, a quick flick with one finger is what the experts
recommend. If this causes the display to flicker then switch off the unit,
remove the power leads, pull back the insulating sleeves, solder along the area
where the wire is crimped by the terminal, and replace them, being careful not
to exchange the 0 and +5 volt connectors.
- It is possible for the ROM sockets to develop
bad contacts. This is sometimes caused by heavy-handed use of the "butterfly"
carrier boards which were used at various stages to put two 8K eproms into one
single 16K socket. The only solution for this is to replace the ROM socket
entirely, and you would be well advised to use the best quality socket
available. This is not an easy task unless you are experienced in the use of
desoldering equipment.
- The most common reason for the cassette system
becoming inoperative is a damaged LM324. Another problem is with the clock input
to the serial processor and it is worth checking that this is the correct
frequency (ie 1.23 MHz = 812 ns periodic time). Another problem which sometimes
occurs is that the value of R75 needs to be changed. The optimum value is
different for different issues of the serial processor ULA because of the
variation in impedence of pin 15 to earth. This affects the timing between
receiving a high tone lead-in and asserting the data-carrier detect on the ACIA.
For ICs numbered 2C199E and 2C199E-3, R75 should be 100k or 56k as required for
consistent loading of data. For 2C199E-7, R75 should be 82k.
- One simple problem, but unfortunately fairly
common, is that the pins of ICs tend to get bent as they are pushed into the
sockets. If you have isolated the fault to a particular area, then this is
something to look out for. It is also not unknown for the IC socket itself to
have a pin bent underneath. This may not have been noticed by quality control if
the IC socket was empty at the time of production eg speech IC
socket.
- If you wish to get two BBC Microcomputers to
send programs to each other on the cassette system, then it is possible to do so
by a direct connection, provided a 1.5k resistor is connected between the signal
line and ground. With the later issue boards that have the 220nF output
capacitor on the cassette system, a smaller value may be necessary. The resistor
is necessary to adjust the relative phase of the two tones of the cassette
signal.
- On a number of occasions, the tracks on the
right hand side of the keyboard PCB have become broken in transit. This occurred
more frequently on earlier versions and less so since the newly modified case
has been used, but if any of the keys on the right hand side are inoperative
then this is a likely cause. Excessively hard use of the keyboard may also cause
solder pads to lift. A group of non-functional keys would indicate that this has
happened. This could be checked quite simply by the use of a meter to test
continuity.
- A number of people complain of interference on
the sound signal. This is caused by the pick up of digital noise as the track
goes from the 1MHz extension bus input to the audio stages. The solution is to
connect a 10k resistor across from this line to ground. This should only be
necessary on issues 1 to 3 of the PCB. It can be done by connecting the resistor
between pin 8 of IC20, which is ground, to the plated-through hole just to the
south of that pin. It is necessary to scratch away the solder resist very
carefully from around this hole, before you can successfully solder into
it.
10k
IC70
IC20
IC86
10k
IC70
IC20
IC86
10k
IC70
IC20
IC86
Pin 8
Plated through
hole
Figure 12 Reducing noise on 1MHz audio
input
- One simple problem that sometimes occurs is
that of getting twinkling characters in some of the higher modes of graphics, or
smeering of the cursor. If this was not originally a problem but has developed
after some months of use, then it may well be that the heat sink on the video
processor has become dislodged. This can be put right by applying firm pressure
to the heat sink and also possibly by applying more heatsink compound between it
and the top of the integrated circuit.
- Certain other faults on the VDU display
associated with the UHF output can be cured by adding extra decoupling to the
supply to the modulator to improve its stability. A 10 ohm series resistor with
a 4.7 uF capacitor to earth is usually sufficient.
- It has been noticed that problems can occur
with some of the 74LS74 ICs, especially from certain manufacturers. If there is
any problem therefore with the cleaness of the clock pulses applied to the
6502A, or problems with the PAL encoder circuit, or more likely with the RAS
signal, it would be worth checking the output of these ICs to see if they are
driving to the full TTL levels.
- Unfortunately, a number of problems also arise
when people have tried to do their own upgrades and have made mistakes or used
bad soldering techniques. In particular, a number of people seem to get the
printer upgrade on the issue 2 board wrong and therefore this should be checked
very carefully (see section 4). Also it is worth checking the soldering very
carefully, particularly around the area of the IDC connectors. This is because
it is easy to get solder bridges over the tracks which are fed in between the
pins on this connector. The worst place seems to be in the area of the tube
connector.
- If there are problems associated with the PAL
or cassette circuitry, it is worth checking very carefully whether the correct
resistor values have been used. Since there are so many resistors so closely
packed together, it is very easy to get resistors in the wrong places. To check
this, it is best to remove the circuit board from the case entirely and use a
strong light source in order to view the resistor's colour codes carefully. This
is well worth doing, as it can save a lot of time looking for faults which are
basically simple but which would be difficult to diagnose.
- Our service centres tell us that there is a
series of rather obscure faults which they have detected which is associated
with timing problems with the RAM. One symptom is twinkling characters in mode 7
but not in the other modes of graphics, and another is that when playing
Acornsoft’s "Defender" (not the later version of "Planetoids") some very
strange effects occur as the game continues. Also there is a program of 3D
Noughts and Crosses from Beebug which produces a strange fault, stopping
inexplicably at one particular line and giving a No Room error. These faults,
being related to relative timing, can sometimes be cured by changing the 6502
processor, or the 74LS245 (IC14) and are more often noticed where the RAM in CAS
1 is a different type from the RAM in CAS 0, when an A to B upgrade has been
done. In particular it seems to be that the Fujitsu RAMs do not mix well with
the Mostek or Hitachi RAMs.
6.5 Test programs
and sample waveforms
6.5.1 Test program
The following program allows you to test the
chip select lines of any of the devices on the computer. It sets up a machine
code loop which accesses the address which you specify as hexadecimal number.
Since it is a closed loop, the only way to escape is to use the break key which
is programmed to re-enter the BASIC program. To escape, enter a zero address. If
you are accessing a slow device, its chip select line should go low for a full
microsecond, but with a fast device, it will only be low for 500 nanoseconds. In
either case, the waveform should be high for 3
microseconds.
10 *KEY10 OLD¦MRUN¦M
20 CLS
30 DIM CODE 20
40 P%=CODE
50 INPUT "ADDRESS",M$
60 M%=EVAL("&" + M$)
70 IF M%=0 THEN END
80 [SEI
90 SEC
100
.again
110
LDA M%
120
BCS again
130
]
140
CALL CODE
The following is a reproduction of a
photograph showing the waveform on pin 23 of the ADC chip, IC73, when the above
test program is running with address &FEC0 selected. Scope parameters are
1V/cm,
1 us/cm.
The following shows pin 24 of the disc
controller chip, IC78, selected by using address &FE80. Scope parameters are
1V/cm, lus/cm.
The following shows two traces while the test
program is running: top trace is 2MHz clock pin 37 IC1, and bottom trace is CAS0
pin 7 IC45. Scope parameters are 2V/cm, 100ns/cm.
The following shows two more traces while the
test program is running: top trace is 2MHz pin 37 IC1, and bottom trace is CAS1
pin 5 IC45. Scope parameters are 2V/cm, 100ns/cm.
The following shows two more traces while the
test program is running. top trace is 2MHz pin 37 IC1, and bottom trace is RAS
pin 12 IC43. Scope parameters are 2V/cm, 100ns/cm.

6.5.2 Test
ROM
The listing shown below is the object code for
a ROM which could prove extremely useful for fault-finding an apparently dead
machine, especially if you do not have a PET. There are three routines given,
but you could extend the idea for up to 8 different routines if you wanted to do
so. The idea is that a 2764 ROM is put in place of the operating system ROM and
the routine which the system starts on
power-up or break is determined by
taking the address lines that would normally be connected to A10, All and A12
(pins 21, 23 and 2 of the 2764 respectively) and have some means of attaching
them to +5 volts or 0 volts.
This can be done crudely by bending up the
three pins so that they don’t engage in the IC socket, and soldering on to
them three leads terminating in crocodile clips. These can then be used to
select the address by clipping on to the +5V and 0V rails, being careful not to
let them short out. For a system that is to be used regularly for fault-finding,
it is wise to use either a DIL switch or better still a thumbwheel switch,
properly mounted.
The three routines given
are:–
Routine "0": Provides a chip select pulse for
each memory-mapped device around the board in turn. The pin numbers at which
each pulse should appear are given in the program.
Routine "1": This sets up the teletext mode of
graphics by programming the 6845 and the video processor appropriately. Then
codes 0 to 255 are stored in the first four pages of video RAM. If there is a
RAM fault then the display will not be the succession of ASCII character which
you would expect, and by careful thought about which characters are in error,
you should be able to diagnose where the problem lies. The pattern is
periodically re-written so that intermittent faults will show up and you can try
temperature exercising any suspect chips.
Routine "2": This is similar to the previous
routine but by incrementing a location on the screen it checks the combination
of reading and writing; ie if the RAM can be written to but not read then the
character at location &7C01 will not cycle through 0 to 255 since the read
instruction will be in error. All these routines are working in machine code at
high speed and therefore it is easy to use an oscilloscope to probe around the
circuit to see what has gone wrong.
10 FOR N% = 0 TO 2 : REM ie 3 tests
available
20 PROCtest(N$)
30 NEXT
40 *SAVE ROMIMAG 3000 +
2000
50 END
60
70 DEFPROCtest(N%)
80 offset% =
&400*N%
90 O% = &3000 +
offset%
100 P% = &F800
110 table% = P% +
&200
120 !(&33FC + offset%) = &F800 : REM
RESET vector
130 opt% = 5
140 IF N% = 0
PROC_strobe_select_lines
150 IF N% = 1
PROC_DRAM_test
160 IF N% = 2
PROC_RNW_exercise
170 !(&3200 + offset%) =
&4433283F
180 !(&3204 + offset%) =
&1B19021E
190 !(&3208 + offset%) =
&13721293
200 !(&320C + offset%) =
&002C002C
210 ENDPROC
220
230
DEFPROC_strobe_select_lines
240 [OPT opt%
250
260 .loop
270 LDA &FE00 \ IC2 pin 25
(CRTC)
280 LDA &FE08 \ IC4 pin 9
(ACIA)
290 LDA &FE10 \ IC7 pin 9 (SER
PROC)
300 LDA &FE18 \ IC96 pin 1 (STATID) or
IC97 pin 4 (INTOFF)
310 LDA &FE20 \ IC97 pin 2
(INTON)
320 STA &FE20 \ IC6 pin 3 (VID
PROC)
330 STA &FE30 \ IC76 pin 9
(ROMSEL)
340 LDA &FE40 \ IC3 pin 23 (VIA
A)
350 LDA &FE60 \ IC69 pin 23 (VIA
B)
360 LDA &FE80 \ IC78 pin 24
(FDC)
370 LDA &FEA0 \ IC89 pin 9
(ADLC)
380 LDA &FEC0 \ IC73 pin 23
(ADC)
390 LDA &FEE0 \ PL 12 pin 8
(TUBE)
400 LDA &FC00 \ PL ll pin 10
(FRED)
410 LDA &FD00 \ PL 11 pin 12
(JIM)
420 JMP loop
430 ]
440 ENDPROC
450
460 DEFPROC_DRAM_test
470 [OPTopt%
480 LDX #&0F
490 STX &FE20 \ Write to
Vidproc
500
510 .setup_6845
520 LDA table%,X \ table of 6845
data
530 STX &FE00 \ Register
number
540 STA &FE01 \ Contents of
register
550 DEX
560 BPL setup_6845
570 LDA #3
580 STA &FEFE \ send down
TUBE
590
600 .restart
610 LDY #0
620
630 .loop2
640 NOP
650 TYA
660 STA &7C00,Y
670 STA &7D00,Y
680 STA &7E00,Y
690 STA &7F00,Y
700 INY
710 BNE loop2
720
730 LDA #&42
740 STA &FE20 \ Write to
Vidproc
750 JMP restart
760 ]
770 ENDPROC
780
790
DEFPROC_RNW_exercise
800
810 [OPT opt%
820 LDX #&0F
830 STX &FE20 \ Write to
Vidproc
840
850 .setup_6845
860 LDA table%,X \ table of 6845
data
870 STX &FE00 \ Register
number
880 STA &FE01 \ Contents of
register
890 DEX
900 BPL setup_6845
910
920 LDA #3
930 STA &FEFE \ send down
TUBE
940
950 LDA #&41 \ Character
"A"
960 LDY #0
970
980 .write
990 INC &7C01 \ Change character on
screen
1000 STA &7D00,Y
1010 STA &7E00,Y
1020 STA &7F00,Y
1030 INY
1040 BNE write
1050
1060 LDA #&42 \ Character
"B"
1070 STA &FE20 \ Write to
Vidproc
1080 JMP write
1090 ]
1100 ENDPROC
The following is a reproduction of a
photograph showing the waveform on pin 34 of the 6502 (R/W of IC1). Scope
parameters are 1V/cm, 2us/cm.
7 Interfacing
Survey
7.1 Purpose of each
interface
Since there are so many different interface
connections on the BBC microcomputer, it may be a help to look at each in turn
and talk about possible applications for each. Working from left to right on the
back of the computer, we start with the UHF output, which provides a PAL colour
TV signal for use with a normal colour television. Next is a video output on a
BNC connector which is intended to be used with a black and white video monitor.
However it is possible to introduce the colour burst information onto this
signal in order to produce a PAL composite video signal. On circuit boards issue
4 onwards, it is possible to introduce this signal by adding a simple link, S39.
On previous issue boards it is necessary to introduce a 470pF capacitor from the
emitter of Q9 to the base of Q7. This capacitor would have to be soldered
directly on to the circuit board.
The third connector which is provided for
video output is a 6-way, 240 degree DIN plug. This provides the red, green, blue
and sync signals needed for an RGB monitor. The sync signal is a 5 volts,
negative going pulse of 4.7uS duration, but it can be changed to positive going
by changing link S31. Also provided on this connector are a 0 volt and a +5 volt
supply, but these should not be used for providing more than a few milliamps to
external circuits.
The next connector is a serial port of the
RS423 standard. This is a standard which has superior drive capabilities to the
RS232 interface and is run in this case between +5 volt and -5 volt levels. The
speed is software selectable at 75, 150, 300, 1200, 2400, 4800 or
9600
baud. There is a higher speed
of 19200 baud, but this is not guaranteed to be error-free. It is also possible
to get the interface to work at 110 baud, but this requires a modification which
would also change the speed of the cassette interface. (See section 7.3 on
hardware hints and tips for more information.) The control signals provided are
the normal CTS and RTS lines, the RTS output also working on +5 volt and -5
volt. NB When making up a connector for the RS423, note that connections as
shown on the circuit diagram refer to the socket. For the plug connections,
refer to page 504 of the User Guide which gives the connections as seen from
outside the case.
Apart from using the RS423 interface to run a
serial printer it is also possible to use it to communicate with other
computers. For example, it is possible to communicate with a mainframe computer
either directly within a building on a wired link or, by using the telephone
network, to a computer in another building or even another country. This would
of course require the use of an acoustic coupler.
There are various levels at which this link
could be used. Firstly the computer could be used as a "dumb terminal”
which would simply be capable of sending characters typed on the keyboard to the
mainframe computer and receiving characters from the mainframe and printing them
on the screen. The following program will allow you to do
so.
10 REM Dumb Terminal
Program
20 REM Only works on OS 1.0 &
following
30 REM Works even if Tube
fitted.
40 REM
50 OSASCI = &FFE3
60 OSBYTE = &FFF4
70 OSWRCH = &FFEE
80 CLS
110 DIM CODE 50
120 FOR J=0 TO 2 STEP
2
130 P%=CODE
140 [OPT J
150 .RS423
160 LDA #&91
170 LDX #1
180 JSR OSBYTE\character in RS423
buffer?
190 BCS keyboard
200 TYA
220 JSR OSWRCH\or OSASCl for
CRLF
230 .keyboard
240 LDA #&91
250 LDX #0
260 JSR OSBYTE\character in keyboard
buffer?
270 BCS RS423
280 TYA
290 JSR OSWRCH\or OSASCI for
CRLF
300 LDA #&8A
310 LDX #2
320 JSR OSBYTE\Put character in RS423
output buffer
330 JMP RS423
340 ]
350 NEXT
360 *FX 7,7
370 *FX 8,7
380 *FX 2,2
390 CLS
400 CALL CODE
The next level would be its use as a
semi-intelligent terminal which would enable you to use some of the processing
of the BBC Microcomputer to deal with file handling, so that the text could be
prepared off line, stored on disc and then spooled down to the mainframe when
the link is made. The third level then would be to use the graphics facilities
of the BBC Microcomputer in addition to its ability to print text. This produces
the possibility of using the computer as a colour-graphics terminal to a
mainframe computer at a fraction of the cost. All that is needed is for someone
to write the appropriate terminal emulation software and put it in sideways ROM.
There are now a number of such packages commercially
available.
The other way in which the RS423 can be used
is to link two BBC computers together. One reason for doing this would be to
enable software to be downloaded from a disc system to another computer which
does not have a disc interface. A 15K program can be downloaded using an RS423
link in approximately 20 seconds which is clearly faster than using a cassette
to cassette link. The only software involved in doing this is to type in, on the
receiving computer:
NEW <RETURN>
*FX2, 1 <RETURN>
(This sets the RS423 as input instead of the
keyboard.)
and then on the sending computer you would
type in:
*FX3,7 <RETURN>
LIST <RETURN>
*FX3,0 <RETURN>
{This enables the RS423 as the output and
sends a listing of the program so that, to the receiving computer, it is as if
it were being typed in from the keyboard.)
If you have a number of transfers to do, then
these commands could be programmed onto a single key on each machine. When the
program has been sent down, you simply have to press BREAK on the receiving
computer, type OLD <RETURN> and then the program is ready for use. If you
are doing a BBC to BBC link over a short distance and want to use the full speed
of the interface then you will have to connect the hand-shake lines as well as
the data lines. The "data out" from one computer should be connected to the
"data in" of the other computer and vice-versa, and in a similar way for the
control lines, the RTS on one should be connected to the CTS on the other and
vice-versa. If you are working over a longer distance and want to use only three
cables, data in, data out, and ground and are prepared to work at a slower speed
without any handshaking, then you have to loop back the RTS to the CTS on each
of the computers so that each is permanently enabled for sending. If you do not
do so, the RS423 output buffer fills up and printing stops after a number of
characters have been sent to the screen.
If you want to use the RS423 interface over a
long distance at high speed using the hand shake lines, it might be necessary to
terminate the receivers by making links S23 and S24. This terminates the line
with its characteristic impedance of 180 ohms.
The cassette interface is a standard CUTS
cassette interface. It has two speeds, 300 and 1200 baud, controllable by
software. There is also motor control provided on pins 6 and 7 of the 7-way DIN
plug. The rating of the relay contacts is 24V at 1A DC, and they should not,
under any circumstances, be used to switch mains voltages, no matter how small
the current. If you wish to get two BBC Microcomputers to send programs to each
other on the cassette system, then it is possible to do so by a direct
connection, provided a 1.5k resistor is connected between the signal line and
ground.
The analogue input is on a 15-way D-type
connector and provides four
A to D
converter channels and two digital input lines which work on the internal 6522
VIA. The pin connections are arranged so that the signals are divided into two
sets intended for use with two games paddles, each of which will have two A to D
inputs and a voltage reference source as well as the ground and one of the
digital input lines.
The conversion time for each channel is 10
milliseconds, but you can choose to have as few or as many of the channels
working as you wish by using the *FX16 command. Therefore if all four converters
are required, you need to allow 40 milliseconds to be sure of a successful
conversion on any one channel. However ADVAL(0) in BASIC, or OSBYTE call 128 in
machine code, can be used to see which channel has just converted, and OSBYTE
call 17 allows you to force a particular ADC channel to convert, out of turn.
The resolution is software selectable between 8 and 12 bits resolution using
OSBYTE 190. However in the 12 bit resolution mode, the true resolution is
somewhat less than 12 bits. It is probably more realistic to think in terms of a
9 or 10 bit accuracy.
Also provided on this connector is an input to
the light pen strobe on the 6845 CRT controller. The hardware involved in
setting up a light pen system is quite simple. The light pen circuit has to
produce a positive-going 5 volt pulse with a duration of greater than 100 ns.
However the software involved is quite complicated if you want to do more than
identify character blocks. This is because of the way in which the 6845 has been
extended beyond its normal memory range in order to provide bit-mapped
graphics.
The final connector which is provided on the
back of the computer is only available when the unit has been upgraded with an
Econet interface. This is a standard 5 pin 180 degree DIN plug to provide the
necessary data and clock signals for the Econet interface.
Underneath the computer is a set of standard
IDC connectors. First of all there is a 34 way connector for the disc drive(s).
This connector carries the standard connections for a 5.25" disc drive. The next
two are a 26-way and a 20-way IDC connector which are used to provide
connections to the two ports of the external 6522 VIA. The 26-way connector
links to port A, and is arranged in a standard format for use with a
Centronics-type parallel printer. The 8 port lines are buffered to provide
better drive capabilities, but it does mean that they can only be used for
output. If you want to use these lines to drive some other device, you should
work on the basis of each line being able to sink 10 mA at logic 0 or to source
400 uA at logic 1. Of the two control lines, CA1 is available as an input with a
single 4k7 pull up resistor on it, whilst the CA2 line is available as an
output, the line being buffered by a single transistor (Q11) to improve the
current sinking. On boards from issue 4 onwards, there is a selection link (S1)
which will enable this line to provide direct connection to CA2 so that it can
be used as either input or output.
The 20-way User Port is much simpler in that
all connections go directly to the lines on the VIA (PB0 to PB7 and also control
lines CB1 and CB2). If you are using these lines for output you should consult
the 6522 data sheet to establish the amount of drive current
available.
The next connector, another 34-way IDC,
provides an extremely versatile interface known as the 1MHz extension bus. This
interface is the subject of a separate Application Note and at this stage it is
sufficient to say that it provides two "pages" (2 x 256 bytes) of memory
locations mapped between &FC00 to &FDFF. By using one of these locations
(&FCFF) as a paging register it is possible to extend the memory addressing
capability to a full 64K bytes.
The final connector is a 40-way IDC which
provides an interface known as the "Tube", intended for use with a second
processor. Although the hardware on the BBC microcomputer side is very simple,
the hardware on the second processor is extremely complex and it really requires
a ULA to incorporate all the hardware necessary to handle the protocol. It is
therefore suggested that any interfacing to the Tube should be done only using
products from Acorn Computers
Ltd.
7.2 Interfacing to various
printers.
It is possible to interface to a wide variety
of printers using the two interfaces provided. First of all, for serial
printers, the RS423 connector can be used and secondly, for parallel printers
the Centronics interface can be used. It is also possible to link up to various
other non-standard printers such as the IEEE 488 printers used for the Commodore
Pet computers. This is more difficult and requires connection not only to the
Printer Port, but also the User Port to provide extra control lines and also
requires extra software within the machine.
It is possible to write your own printer
driver routine which works through the operating system.
In order to link up to teletype printers,
which run at 110 baud, you have to change the position of link S28. This is
explained in detail in section 7.3.
One important point to note is that on issue 1
printed circuit boards, the pin connections on the printer port are not quite
the same as later issues. Pin 19 is the ACK line and pin 26 is not open circuit
as it should be for certain printers. If you wish to use this interface, for
example with the Seikosha GP80A, you will encounter problems since pin 26 is
used as a reset line. Another problem which may occur on the early issue boards
is that there is no pull-up resistor on the CA2 line thus leaving the collector
of transistor Q11 open circuit.
7.3 Hardware Hints
and Tips
Here are a number of miscellaneous hints and
tips which have come from various sources.
In order to get the
RS423 interface to work at 110 baud, all that has to be done is to use the
*FX8,1 command in order to set 75 baud and then change the position of link S28.
This link is made by a track on the PCB, between the centre pin and the west
pin. This link has to be broken and a solder link made from the centre pin to
the east pin. This has the effect of speeding up all of the baud rates, both
send and receive by 44%, and also makes the cassette port run fast by the same
amount, so a single pole double throw switch could be wired to S28 in order to
select the normal speed or the fast speed for the 110 baud. The actual speed
produced is 108.333 but this is near enough for most teletype
printers.
KEYBOARD
CONNECTOR
74LS251
Break link here
For certain applications, particularly when
the computer is being used by very young children, it is most frustrating when
the user presses the break key. It is easy enough to disable the escape key
within a program, but the break key is more of a problem. You could use *KEY10
OLD¦M RUN¦M but even this is not very satisfactory. The alternative is
to disable the break key electrically, which can be done by removing a link from
the keyboard PCB. You could then wire it up to a miniature ON-OFF toggle switch
which can be mounted on the back of the case by drilling a suitable hole, or
leave it open circuit and use the contacts at the back of the main PCB marked
"RST SW", to provide an alternative break key. The disadvantage of doing this
though is that if you are using a disc system, you may want to be able to do a
SHIFT break in order to boot the disc. The position of the link to be removed is
shown below.
Figure 13 Disabling the BREAK
key
8 Component location
tables
The following lists of components should
enable you to locate any component on the main circuit diagram by its X and Y
grid reference (see grid numbers on main PCB circuit diagram). For ICs and
selection links, their positions on the PCB itself are also given. These are
defined by X and Y coordinates in millimetres, measuring from the SW corner of
the PCB.
8.1 Integrated circuits
NB Some ICs which contain more than one
circuit will appear at more than one place on the circuit
diagram.
IC Type PCB Circuit Comments
Position Diagram
1 6502A 160,85 10,6
2 6845 160,140 5,3 CRT
controller
3 6522 90,75 5,9 Internal
VIA
4 6850 128,141 11,5 ACID
5 SAA5050 187,102 10,2 Teletext
ROM
6 5C094 214,71 7,6 10,1 Video
ULA
7 2C199 128,182 12,4 Serial
ULA
8 81L595 241,62 5,1
9 81LS95 241,93 5,2
10 81LS95 252,63 5,3
11 81LS95 252,93 5,4
12 81LS95 275,62 5,4
13 81LS95 264,62 5,5
14 74LS245 184,71 9,4
15 74LS273 196,71 9,2
16 LM555 7,210 6,7
17 LM324 6,28 4,6
18 76489 22,44 5,6 Sound
generator
19 LM386 52,23 5,5
20 74LS139 120,23 7,10
9,8
21 74LS00 120,55 10,8
22 74LS30 137,55 6,10
23 74LS30 120,80 8,9
24 74LS138 135,78 6,10
25 74LS20 120,108 7,10
10,6
26 74LS139 137,105 6,8
27 7438 3,124 2,4 4,2 4,10
12,7
28 74LS51 50,143 7,7
9,6
29 74LS32 65,143 5,6 8,7
8,8
30 74LS74 78,143 8,6
31 74LS34 90,143 5,9
8,7
32 74LS259 105,143 5,10
33 74LS04 58,164 4,9 10,9
10,3
34 74LS74 71,164 8,7
35 LM324 151,205 13,5
36 74LS10 215,122 4,2
10,3
37 74LS04 228,122 8,6 10,3
10,6
38 74LS86 241,122 5,3
39 74LS283 197,145 5,2
40 74S00 206,149 4,2 6,5 8,6 (Previously
74LS00)
41 74LS02 228,149 4,4
7,4
42 74LS163 241,158 12,6
43 74S04 187,174 7,6
8,4
44 74LS74 206,174 12,1
45 74S139 228,172 7,5
46 74S74 252,183 12,2
47 74LS86 264,183 13,2
48 74LS86 275,183 13,1
49 74LS00 286,183 13,2
50 74LS00 298,183 12,6
13,1
51 (27128) 214,24 8,9 Operating system
ROM
52 (27128) 233,24 9,9 BASIC
ROM
53 4816 287,69 8,2
54 4816 287,93 8,2
55 4816 275,93 8,3
56 4816 298,146 8,4
57 4816 287,146 8,2
58 4816 275,146 8,2
59 4816 264,146 8,3
60 4816 252,146 8,4
61 4816 298,68 6,2
62 4816 298,93 6,2
63 4816 264,93 6,3
64 4816 298,122 6,4
65 4816 287,122 7,2
66 4816 275,122 7,2
67 4816 264,122 7,3
68 4816 252,122 7,4
69 6522 160,29 2,6 External
VIA
70 74LS244 137,24 2,6
71 74LS244 184,29 2,4
72 74LS245 199,29 2,3
73 uPD7002 100,173 14,6 ADC
convertor
74 88LS120 183,201 13,4
75 3691 207,199 14,4
76 74LS163 70,44 10,8
77 74S00 38,143 4,8 4,9
78 8271 60,75 3,9 Disc
controller
79 7438 42,46 2,9
80 7438 57,46 2,9
81 74LS393 82,46 2,8
82 74LS10 97,46 3,8
83 4013 67,24 4,7
84 4013 82,24 3,7
85 4020 97,21 2,7
86 74LS393 108,23 2,7
87 74LS123 43,164 2,10
13,8
88 2764 252,24 9,9
89 68B54 15,125 12,8 ADLC –
Econet
90 40178 16,162 13,10 (Not
fitted)
91 74LS132 27,166 12,7
14,9
92 74LS74 16,188 14,10 (Not
fitted)
93 75159 13,166 14,9
94 LM319 45,93 13,8
95 LM319 20,193 13,7
96 74LS244 82,185 12,10
97 74LS74 4,171 13,9
98 TMS6100 15,75 4,8 Speech
ROM
99 TMS5220 35,75 5,7 See Speech
generator
100 (27128) 272,24 10,9 Sideways
ROM
101 (27128) 290,24 11,9 Sideways
ROM
8.2
Transistors
Q Type Circuit
Diagram
1 BC239 13,5
2 BC239 13,5
3 BC239 13,5
4 BC239 11,3
5 BC239 12,3
6 BC239 12,3
7 BC309 14,2
8 BC309 13,2
9 BC239 14,1
10 2N3906 11,2
11 BC239 2,4
8.3 Diodes
D Type Circuit
Diagram
1 1N4148 6,8
2 1N4148 4,6
3 1N4148 14,7
4 1N4148 10,8 Not
fitted
5 1N4148 10,8 Not
fitted
6 1N4148 14,6
7 1N4148 14,6
8 1N4148 14,6
9 1N4148 12,5 Not
fitted
10 1N4148 8,8 Not fitted, issue 7
onwards
11 1N4148 8,8 Not fitted, issue 7
onwards
12 1N4148 8,8 Not fitted, issue 7
onwards
13 1N4148 13,5
14 1N4148 3,3
15 1N4148 3,3
16 1N4002 11,1
17 1N4002 11,1
18 1N4002 11,1
19 1N4148 13,1
20 1N4148 13,3
21 1N4148 13,3
22 1N4148 13,3
8.4 Capacitors
C Type Circuit
Diagram
1 2n2F Plate
ceramic 4,6
2 4u7F 16V Elec 4,5
3 2n2F Plate
ceramic 4,6
4 Not used
5 l0uF 16V Elec 4,5
6 100nF Disc ceramic 6,7
7 2n2P Plate ceramic 4,5
8 100nF Disc
ceramic 6,7
9 10uF 16V Elec 4,4
10 10nF Plate
ceramic 6,7
ll 2n2F Plate
ceramic 4,5
12 10pF Plate
ceramic 5,7
13 lnF Plate
ceramic 2,10
14 47uF 10V Elec 3,1
15 100nF Disc
ceramic 5,5
16 47uF 10V Elec 5,5
17 2n2F Plate
ceramic 13,9
18 10uF 10V Tant 14,8
19 Not used
20 47nF Disc ceramic 5,5
21 100nF Disc
ceramic 5,7
22 Net used
23 10nF Plate
ceramic 13,8
24 100nF Disc
ceramic 6,7
25 33nF Polyester 14,6
26 47uF l0V Elec 4,1
27 luF 35V Tant 14,6
28 4u7P 10V Tant 12,5
29 2n2F Plate
ceramic 13,5
30 10uF 10V Tant 12,5
31 820pF Plate
ceramic 15,5
32 4n7F Plate
ceramic 14,5
33 4n7F Plate
ceramic 13,5
34 200/220nF 14,5
35 820pF Plate
ceramic 15,5
36 47uF l0V Tant 4,1
37 33pF Plate
ceramic 6,6
38 2n2F Plate
ceramic 13,3
39 2n2F Plate
ceramic 13,3
40 10nF Plate
ceramic 7,6
41 220pF Plate
ceramic 8,5
42 33pF Plate
ceramic 6,5
43 47pF Plate
ceramic 14,4
44 Not used
45 10nF Plate
ceramic 13,1
46 47pF Plate
ceramic 14,4
47 10uF 10V Tant 11,1
48 270pF Plate
ceramic 8,5
49 150pF
Plate ceramic 13,2
50 47pF Plate
ceramic 14,2
51 15/22pF Plate
ceramic 11,2 (SOT)
52 390pF Plate
ceramic 11,2
53 100pP Plate
ceramic 11,2
54 47uF 10V Tant 4,1
55 100pF Plate
ceramic 11,1
56 39pF Plate
ceramic 14,1
57 10uF 10V Tant 3,1
58 470pF Plate
ceramic 14,2
59 220nF 13,5
60 4u7F 10V Tant 3,1
8.5
Resistors
R Value Circuit
Diagram
1 10k 4,6
2 10k 5,6
3 10k 5,6
4 22k 4,6
5 100k 3,6
6 4k7 1,5
7 100k 3,6
8 10k 4,5
9 39k 4,6
10 3k3 4,2
11 100k 3,6
12 220k 3,6
13 1M 6,7
14 10R 4,5
15 39k 3,5
16 22k 4,5
17 10k 4,5
18 10R 4,4
19 Not used
20 1M 6,8
21 1M 6,7
22 150R 3,9
23 150R 3,9
24 39k 4,4
25 Not used
26 Not used
27 10k 3,5
28 4k7 3,5
29 1k 3,5
30 10k 5,6
31 4k7 5,6
32 150k 5,7
33 1k 2,10
34 10k (2%) 14,8
35 10k (2%) 14,8
36 1M5 13,8
37 1k 2,9
38 100K (2%) 14,8
39 100K (2%) 14,8
40 100K (2%) 14,8
41 100K (2%) 14,8
42 Not used
43 Not used
44 1M5 13,9
45 10k (2%) 13,8
46 1k 13,8
47 1k5 (2%) 14,8
48 1k (2%) 14,8
49 150R 2,10
50 39k 12,9
51 10k (2%) 14,8
52 1k 13,9
53 1k 4,7
54 Not used
55 3k3 8,8 Not fitted, issue 7
onwards
56 Not used
57 10R 5,5
58 150R 1,7
59 56k (2%) 13,7
60 56k (2%) 13,7
61 1k 13,8
62 56k (2%) 13,7
63 56k (2%) 13,7
64 1M5 13,7
65 3k3 3,10
66 10k 5,10
67 10k 5,10
68 3k3 2,7
69 3k3 10,8
70 3k3 2,6
71 2k7 14,6
72 3k3 8,9 Not fitted, issue 7
onwards
73 3k3 7,9 Not fitted, issue 7
onwards
74 2k2 12,5
75 82k 12,5
76 10k 13,5
77 100k 13,5
78 150k 14,4
79 820k 15,5
80 39k 14,5
81 3k3 10,6
82 150k 14,4
83 4k7 5,4
84 10k 13,5
85 3k3 10,6
86 220k 14,S
87 8k2 14,5
88 8k2 14,5
89 4k7 13,4
90 4k7 13,5
91 820R 7,6
92 820R 7,6
93 3k3 14,4
94 100R 8,6
95 2k2 14,4
96 3k3 14,4
97 2k2 14,4
98 1k2 7,5
99 1k2 10,2
100 1k2 11,2
101 1k0 11,2
102 100R 6,5
103 1k0 10,2
104 100R 9,8 Not fitted, issue 4
onwards
105 100R 8,6
106 56R 8,4
107 1k0 7,5
108 3k3 3,3
109 1k8/2k7 13,1 SOT
110 68R 14,2
111 68R 14,3
112 68R 14,3
113 68R 14,3
114 18R 1W 12,1
115 1k0 14,2
116 3k9 14,2
117 2k2 14,2
118 1k0 14,2
119 100R 8,5
120 82R 12,3
121 82R 11,3
122 82R 11,3
123 470R 14,2
124 56R 7,4
125 100R 9,8 Not fitted, issue 4
onwards
126 3k9 14,1
127 1k5 14,2
128 470R 13,2
129 68R 14,2
130 68R 13,2
131 56R 7,4
132 120k 14,1
133 120k 14,1
134 1k0 14, 2
135 1k0 14, 1
136 2k2 13,3
137 3k9 13,2
138 1k5 13,2
139 1k0 13,2
140 1k0 14,2
141 2k7 14,2
142 100R 9,8 Not fitted, issue 4
onwards
143 12k 11,2
144 15k 11,2
145 1k0 11,2
146 1k5 11,1
147 3k9 11,1
14S 820R 14,2
149 100R 9,8 Not fitted, issue 4
onwards
150 680R 14,2
151 470R 14,1
152 2k2 14,2
153 100R 9,8 Not fitted, issue 4
onwards
154 1k2 14,1
155 680R 14,1
156 3k3 14,1
157 680R 14,1
158 470R 14,1
159 270k 13,5
160 3k3 12,4
161 5k6 13,4
162 4k7 1,6
163 Not used
164 Not used
165 Not used
166 Not used
167 Not used
168 Not used
169 Not used
170 2k2 2,5
171 100R 13,6
172 10k 4,6
173 4k7 12,8
174 22k 12,3
8.6
Links
Some links have been omitted on later issue
boards, while others have been added.
LINK PCB Circuit
position diagram
1. 2,108 2,5 (Not used on issues 2 and
3)
2. 2,161 12,7
3. 2,173 14,14 (Only fitted on issues
1,2,3)
4. 12,12 1,9
5. 26,195 14,9 (Only fitted on issues
1,2,3)
6. 26,205 15,9 (Only fitted on issues
1,2,3)
7. 30,65 4,9
8. 32,15 2,9
9. 35,128 3,10
10. 45,15 1,8
11. 75,210 13,10
12. 97,70 9,8
13. 100,67 9,8
14. 101,53 7,10
15. 107,97 7,9
16. 108,90 7,9
17. 108,52 7,10
18. 110,52 7,8
19. 102,102 7,8
20. 123,55 9,8
21. 122,65 9,8
22. 127,70 9,8
23. 177,215 13,3
24. 181,195 13,3
25. 215,185 7,5
26. 221,68 10,1
27. 226,95 1,7
28. 237,144 12,6
29. 237,146 12,6
30. 284,20 8,8
31. 270,170 14,3
32. 295,65 9,9
33. 295,67 10,9
34. 200,65 9,8 (From issue 4
onwards)
35. 245,20 9,8 (From issue 4
onwards)
36. 260,20 9,8 (From issue 4
onwards)
37. 280,20 9,8 (From issue 4
onwards)
38. 300,15 9,8 (From issue 4
onwards)
39. 255,215 9,8 (From issue 4
onwards)
9
Appendices
9.1 Circuit block
diagram
9.2 Assembly
drawing
9.3 Case Lower
Assembly
Drawing
9.4 Main PCB
layout
9.5 Main PCB Circuit
Diagram
9.6 Keyboard circuit
diagram
9.7 Power supply
circuit
diagram
9.8
Parts list
CASE LOWER ASSEMBLY MDDEL B + ECONET +
DISC
ITEM PART
No DESCRIPTION QTY REMARKS
1 A2/210,232 CASE
LOWER 1
2 A2/103,500 MAIN
PCB ASSEMBLY HDDEL B+ECONET+DISC 1
3 A1/103,004/A CASE
LOWER ASSY REF 'STANDARD' DRG
4 A1/103,001 KEYBOARD
ASSEMBLY (INC SPKR) 1
5 A2/201,111 CUT
RIGID PVC LABEL BOTTOM ACCESS 1
6 A2/201,098 CUT
RIGID PVC LABEL REAR ACCESS 1
7
8 890,000 STICK
ON FEET 4
9
10 800,600 B.N.C.
CONNECTOR 75R 1 PANEL MOUNT SK2
11 870,109 WIRE
7/0,2 WHITE PVC 2 2" LENGTH
12
13 882,644 No
8 x 9.5 FLANGE HEAD POSIDRIV 5 BLACK SELF TAP
14 882,712 No
4 x 7/16" PAN HD SUPERDRIVE 2 PLASTITE
15 882,986 NYLON
WASHER I/D 5mm 5
16
17
18
19 882,022 M3
x 5mm CHEESE HEAD POSI DRIVE 3 USE WITH ITEM 24
20
21
22
23
24 103,003 POWER
SUPPLY UNIT 1 ASTEC SMPS
25
26
27 882,988 4
BA INTERNAL T00TH SHAKEPR00F WASHER 2
28 882,914 4BA
NUT FULL 2
29 882,343 4BA
x 5/8" PAN HD POSIDRIV 2
30
MAIN
CIRCUIT BOARD MODEL B + DISC + ECONET
ITEM PART
No DESCRIPTION QTY REMARKS
1 203000 PRINTED
CIRCUIT BOARD 1
2 103,500/A ASSEMBLY
DRAWING MODEL B +DISC+ECONET 1 PER WORKS ORDER
3
4 520,180 RESISTOR
18R 1W 10% CARBON FILM 1 R114
5
6 500,100 RESISTOR
10K 1/4W l0% CARBON FILM 3 R14,18,57
7 500,560 RESISTOR
56R 10% CARBON FILM 3 R106,124,131
8 500,680 RESISTOR
68R 1/4W 10% CARBON FILM 6 R110,113,129,130
9 500,820 RESISTOR
82R 1/4W 10% CARBON FILM 3 R120,121,122
10 500,101 RESISTOR
100R 1/4W 10% CARBON
FILM 5 R94,102,105,119,
171
11 500,151 RESISTOR
150R 1/4W 10% CARBON FILM 4 R22,23,49,58
12 500,471 RESISTOR
470R 1/4W 10% CARBON FILM 4 R123,128,151,158
13 500,681 RESISTOR
680R 1/4W 10% CARBON FILM 3 R150,155,157
14 500,821 RESISTOR
820R l/4W 10% CARBON FILM 3 R91,92,148
15
16 500,102 RESISTOR
1K 1/4W 10% CARBON
FILM 20 R29,33,37,46,52,
53,61,101,103,
107,115,118,134,
135,139,140,145, 98,99,100
17
18
19 500,122 RESISTOR
1K2 1/4W 10% CARBON FILM 2 R154,127
20 500,152 RESISTOR
1K5 1/4W 10% CARBON FILM 2 R138,146
21 500,222 RESISTOR
2K2 1/4W 10% CARBON
FILM 7 R74,95,97,117,
136,152,170
22 500,272 RESISTOR
2K7 1/4W 10% CARBON FILM 1 R71
23 500,332 RESTSTOR
3K3 1/4W 10% CARBON
FILM 12 R10,65,68,69,70,
81,85,93,96,108,
156,160
24
25 500,182 RESISTOR
1K8 1/4W 10% CARBON FILM 1 R141
26 500,392 RESISTOR
3K9 10% CARBON FILM 4 R116,126,137,147
27 500,472 RESISTOR
4K7 1/4W 10% CARBON
FILM 8 R6,28,31,83,89,
90,162,173
28 500,562 RESISTOR
5K6 1/4W 10% CARBON FILM 1 R161
29 500,822 RESISTOR
8K2 1/4W 10% CARBON FILM 2 R87,88
30
31 500,103 RESISTOR
10K 1/4W 10% CARBON
FILM 12 R1-3,8,17,27,30,
66,67,76,84,172
32
33 500,123 RESISTOR
12K 1/4W 10% CARBON FILM 1 R143
34 500,153 RESISTOR
15K 1/4W 10% CARBON FILM 1 R144
35 500,223 RESISTOR
22K 1/4W 10% CARBON FILM 3 R4,16,174
36 500,393 RESISTOR
39K 1/4W 10% CARBON FILM 5 R9,15,24,50,80
37 500,823 RESISTOR
82K 1/4W 10% CARBON FILM 1 R75
38 500,104 RESISTOR
100K 1/4W 10% CARBON FILM 4 R5,7,11,77
39 500,124 RESISTOR
120K 1/4W 10% CARBON FILM 2 R132,133
40 500,154 RESISTOR
150K 1/4W 10% CARBON FILM 2 78,82
41
42 500,224 RESISTOR
220K 1/4W 10% CARBON FILM 2 R12,86
43 500,274 RESISTOR
270K 1/4W 10% CARBON FILM 1 R159
44 500,824 RESISTOR
820K 1/4W 10% CARBON FILM 1 R79
45
46 500,105 RESISTOR
1M 1/4W 10% CARBON 3 R13,20,21
47 500,155 RESISTOR
1M5 1/4W 101 CARBON 3 R36,44,64
48 590,682 RESISTOR
PACK S.I.P. 6K8 x 8 1 RP1
49 590,223 RESISTOR
PACK S.I.P. 22K x 8 1 RP2
50 580,103 POTENTIOMETER
10% VERT. MIN. PRESET 1 VR1
51 580,204 POTENTIOMETER
200K VERT. MIN. PRESET 1 VR2
52
53 500,182/272 RESISTOR
1K8/2K7 1/4W 10% CARBON FILM 1 R109,S.O.T.
ON
BATCH
BASIS
54
55 505,102 RESISTOR
1K 1/4W 2% CARBON 1 R48
56 505,152 RESISTOR
1K5 1/4W 2% CARBON 1 R47
57 505,103 RESISTOR
10K 1/4W 2% CARBON 4 R34,35,45,51
58 505,563 RESISTOR
56K 1/4W 2% CARBON 4 R59,60,62,63
59 505,104 RESISTOR
100K 1/4W 2% CARBON 4 R38,39,40,41
60
61 631,010 CAPACITOR
10pF PLATE CERAMIC 1 C12
62 631,015/022 CAPACITOR
15/22pF PLATE CERAMIC 1 C51,S.O.I.
ON
BATCH
BASIS
63 631,033 CAPACITOR
33pF PLATE CERAMIC 2 C37,42
64 631,039 CAPACITOR
39pF PLATE CERAMIC 1 C56
65 631,047 CAPACITOR
47pF PLATE CERAMIC 1 C50
66 631,100 CAPACITOR
100pF PLATE CERAMIC 2 C53,55
67 631,150 CAPACITOR
150pF PLATE CERAMIC 1 C49
68
69 631,220 CAPACITOR
220pF PLATE CERAMIC 1 C41
70 631,270 CAPACITOR
270pF PLATE CERAMIC 1 C48
71 630,039 CAPACITOR
390pF PLATE CERAMIC 1 C52
72 630,082 CAPACITOR
820pF PLATE CERAMIC 2 C31,35
73 632,047 CAPACITOR
47pF PLATE CERAMIC 2 C43,46
74 633,047 CAPACITOR
470pF PLATE CERAMIC 1 C58
75 629,001 CAPACITOR
lnF PLATE CERAMIC 1 C13
76 629,002 CAPACITOR
2n2F PLATE CERAMTC 6 C1,3,7,11,17,29
77 634,004 CAPACITOR
4n7F PLATE CERAMIC 2 C32,C33
78 629,010 CAPACITOR
10nF PLATE CERAMIC 4 C10,23,40,45
79 650,333 CAPACITOR
33nF POLYESTER 1 C25
80 680,001 CAPACITOR,
DECOUPLER 33/47 nF 76 A
81 628,470 CAPACITOR
47nF DISC CERAMIC 1 C20
82 628,101 CAPACITOR
100nF DISC CERAMIC 5 C6,8,15,21,24
83 634,002 CAPACITOR
2n2F PLATE CERAMIC 2 C36,39
84 651,224 CAPACITOR
220nF 1 C59
85 613,100 CAPACITOR
luF 35V TANTALUM 1 C27
86 610,005 CAPACITOR
4u7F 10V TANTALUM 2 C28,60
87 635,047 CAPACITOR
4u7F 16V RADIAL ELEC 1 C2
88 610,010 CAPACITOR
10uF 10V TANTALUM 4 C18,30,47,57
89 635,100 CAPACITOR
10uF 16V RADIAL ELEC 2 C5,9
90 610,047 CAPACITOR
47uF 10V TANTALUM 2 C36,54
91 621,470 CAPACITOR
47uF 10V AXIAL ELEC 3 C14,16,26
92 651,204/224 CAPACITOR
200/220nF 1 C34
93
94 699,001 TRIMMING
CAPACITOR 2-22pF 1 VC1
95
96
97 860,005 CHOKE
33 uH 1 L1
98
99
100 820,160 CRYSTAL
16 MHz 1 X1
101 820,177 CRYSTAL
17,7345 MHz 1 X2
102
103
104 794,002 DIODE
IN 4002 3 D16,17,18
105 794,148 DIODE
IN
4148 12 D1,2,6,7,8,
13-l5,19-22
106
107
108 810,001 RELAY
5V 1 RL1
109
110
111 780,239 TRANSISTOR
BC 239 8 Q1-6,9,11
112 780,309 TRANSISTOR
BC309 2 Q7,8
113 783,906 TRANSISTOR
2N3906 1 Q16
114
115
116 800,114 I.C.
SOCKET D.I.L. 14 PIN 4 55,94,95,93
117 800,120 I.C.
SOCKET D.I.L. 20 PIN 1 IC14
118
119 800,128 I.C.
SOCKET D.I.L. 28
PIN 11 IC6,7,51,52,73,
89,98,99,100,101
120 800,140 I.C.
SOCKET D.I.L. 40 PIN 5 IC1-3,69,78
121 740,038 INTEGRATED
CIRCUIT 7438 3 IC27,79,80
122 741,000 INTEGRATED
CIRCUIT 74S00 1 IC40
123 742,000 INTEGRATED
CIRCUIT 74LS00 4 IC21,49,50,77
124 742,002 INTEGRATED
CIRCUIT 74LS02 1 IC41
125 741,004 INTEGRATED
CIRCUIT 74S04 1 IC43
126 742,004 INTEGRATED
CIRCUIT 74LS04 2 IC33,37
127 742,010 INTEGRATED
CIRCUIT 74LS10 2 IC36,82
128 742,020 INTEGRATED
CIRCUIT 74LS20 1 IC25
129 742,030 INTEGRATED
CIRCUIT 74LS30 2 IC22,23
130 742,032 INTEGRATED
CIRCUIT 74LS32 1 IC29
131 742,051 INTEGRATED
CIRCUIT 74LS51 1 IC28
132 741,074 INTEGRATED
CIRCUIT 74S74 1 IC46
133 742,074 INTEGRATED
CIRCUIT 74LS74 5 IC30,31,34,44,97
134 742,086 INTEGRATED
CIRCUIT 74LS86 3 IC38,47,48
135 742,138 INTEGRATED
CIRCUIT 74LS138 1 IC24
136 241,139 INTEGRATED
CIRCUIT 74S139 1 IC45
137 742,139 INTEGRATED
CIRCUIT 74LS139 2 IC20,26
138 742,163 INTEGRATED
CIRCUIT 74LS163 2 IC42,76
139 742,244 INTEGRATED
CIRCUIT 74LS244 3 IC70,71,96
140 742,245 INTEGRATED
CIRCUIT 74LS245 2 IC14,72
141 742,259 INTEGRATED
CIRCUIT 74LS259 1 IC32
142 742,273 INTEGRATED
CIRCUIT 74LS273 1 IC15
143 742,283 INTEGRATED
CIRCUIT 74LS283 1 IC 39
144 770,324 INTEGRATED
CIRCUIT LM324 2 IC17,35
145 770,386 INTEGRATED
CIRCUIT LM386 1 IC19
146 770,555 INTEGRATED
CIRCUIT LM555 1 IC16
147 738,095/097 INTEGRATED
CIRCUIT 81LS95/97 2 IC12,13
148 706,489 INTEGRATED
CIRCUIT 76489 1 IC18
149 738,095 INTEGRATED
CIRCUIT 81LS95 4 IC8-11
150 739,120 INTEGRATED
CIRCUIT 88LS120 1 IC74
151 706,502 INTEGRATED
CIRCUIT 6502A 1 IC1
152 706,522 INTEGRATED
CIRCUIT 6522 2 IC3,69
153 706,845 INTEGRATED
CIRCUIT 6845 1 IC2
154 706,850 INTEGRATED
CIRCUIT 6850 1 IC4
155 733,691 INTEGRATED
CIRCUIT 3691 1 IC75
156 705,050 INTEGRATED
CIRCUIT SAA5050 1 IC5
157 201,601/647 INTEGRATED
CIRCUIT VIDEO PROCESSOR 1 IC6
158 201,602/648 INTEGRATED
CIRCUIT SERIAL PROCESSOR 1 IC7
159 707,002 INTEGRATED
CIRCUIT 7002 1 IC73
160 704,816 INTEGRATED
CIRCUIT 4816 16 IC53-68
161 201,629 INTEGRATED
CIRCUIT 23128 1 IC51 (OPERATING SYSTEM)
162 201,628 INTEGRATED
CIRCUIT 23128 1 IC52 (BASIC)
163
164 800,004 SOCKET
D.I.N. 5 WAY 1 SK7
165 825,000 SOCKET
UM1233-E36 1 SK1
(UHF
MODULATOR)
166 800,002 SOCKET
D.I.N. 6 WAY 1 SK3
167 800,001 SOCKET
D.I.N. 5 WAY DOMINO 1 SK4
168 800,003 SOCKET
D.I.N. 7 WAY 1 SK5
169 800,304 SOCKET
'D' TYPE 15 WAY 1 SK6
170
171 800,059 PLUG
17 WAY 1 PL13 (KEYBOARD)
172 800,055 PLUG
10 WAY 1 PL14 (SERIAL ROM)
173 800,050 PLUG
2 WAY 4 PL15 S21(2),39
174 300,051 PLUG
3
WAY 7 S20,32,25,26,
31-33
175 800,070 SHUNT
16 S20,21(2),22,25,
26,31-33,S11(7)
176 800,054 PLUG
8 WAY 2 S11
177 880,040 SLEEVING
BLACK NEOPRENE A/R FIT TO R114
178 201,029 HEATSINK 1 FIT
TO IC6
IF
201,601
179 870,420 WIRE
TCW A/R 18(N),19(E)
180 800,200 FASHION
TAB 7
181 800,006 CONNECTOR
IDC 34 WAY 2 PL8,11
182 800,008 CONNECTOR
IDC 26 WAY 1 PL9
183 800,009 CONNECTOR
IDC 20 WAY 1 PL10
184 800,007 CONNECTOR
IDC 40 WAY 1 PL12
185
186 742,123 INTEGRATED
CIRCUIT 74LS123 1 IC87
187 742,132 INTEGRATED
CIRCUIT 74LS132 1 IC91
188 742,393 INTEGRATED
CIRCUIT 74LS393 2 IC81,86
189 735,159 INTEGRATED
CIRCUIT 75159 1 IC93
190 706,854 INTEGRATED
CIRCUIT 68B54 1 IC 89
191 754,013 INTEGRATED
CIRCUIT 4013 2 IC83,84
192 754,020 INTEGRATED
CIRCUIT 4020 1 IC85
193 708,271 INTEGRATED
CIRCUIT 8271 1 IC78
194 770,319 INTEGRATED
CIRCUIT LN319 2 IC94,95
195 201,666 INTEGRATED
CIRCUIT 27128* 1 IC88 (DNFS ROM)
9.9
Glossary of abbreviations
ACK ACKnowledge
line on the printer port
ACTA Asynchronous
Communications Interface Adaptor – serial to parallel and parallel to
serial converter (6850)
ADC Analogue
to Digital Converter
ADLC Advanced
Data Link Controller – Econet control IC (68B54)
ADSR Attack,
Decay, Sustain, Release – defining the envelope of
a sound
ASCII American
Standard Code for Information Interchange – binary code for representing
alphanumeric characters.
BASIC Beginners
All-purpose Symbolic Instruction Code
BBC British
Broadcasting Corporation
BNC Bayonet-Neill-Concelman
– the type of bayonet connector
used for the video
output
CA1/2 Control
lines associated with the PA port on a VIA
CAS Column
Address Strobe – control line for the dynamic RAM
CAS0 Refers
to the area of RAM selected by the CAS0 line
CAS1 Refers
to the area of RAM selected by the CAS1 line
CB1/2 Control
lines associated with the PB port on a VIA
CP/M Control
Program for Microcomputers - Z80 based operating system
CPU Central
Processor Unit (6502)
CR Capacitor
Resistor network
CRT Cathode
Ray Tube
CRTC Cathode
Ray Tube Controller IC (6845)
CSYNC Composite
SYNChronisation pulse from the CRTC
CTS Clear
To Send – control input on the RS423 port
CUTS An
American standard for frequency shift keying – ie using
two different tones to represent
logic levels
DIN Connectors
such as the cassette socket, RGB socket etc
DRAM Dynamic
RAM
EPROM Erasable
Programmable Mead Only Memory
FIT Final
Inspection Tester
FDC Floppy
Disc Controller (8271)
IC Integrated
Circuit
ID IDentity
– refers to the unique number of a given Econet
station
IDC Insulation
Displacement Connectors – parallel cable connectors underneath the
computer
IEEE488 A
parallel interface usually associated with automatically controlled test
instruments
I/O Input
Output
IRQ Interrupt
ReQuest – control line on the 6502 processor
LK PCB
link
MA0-13 Memory
Access – control lines out of the CRTC
MOS Machine
Operating System
MPU Microprocessor
Unit
NMI Non-Maskable
Interrupt – control line on the 6502 processor
PA Port
A – One of the two ports of a VIA
PAL Phase
Alternation Line – coding method used for combining separate colour
information into a single signal
PB Port
B – The other port of a VIA
PCB Printed
Circuit Board
PET Progressive
Establishment Tester
PL Header
plug
PSU Power
Supply Unit
Q1
etc Transistor numbers
QWERTY These
are the upper left keys on the keyboard ie refers to the standard keyboard
layout
RA0-2 Row
Address lines from the CRTC to access the RAM
RAM Random
Access read/write Memory
RAS Row
Address Strobe – Control line for the DRAM
RC Resistor
Capacitor network
RGB Red
Green Blue – individual colour signals for the VDU
ROM Read
Only Memory
ROMSEL ROM
SELect latch
RS423C An
internationally defined convention for serial transmission of
data
RTS Ready
To Send – control output on RS423 port
SK Socket
SOT Select
On Test
SW South
West
TCW Tinned
Copper Wire
TTL Tranistor
Transistor Logic – a standard type of digital IC (74-
series)
UHF Ultra
High Frequency – signal for input to a TV aerial
socket.
ULA Uncommitted
Logic array – semi-custom IC
VDU Visual
Display Unit
VIA Versatile
Inter ace Adaptor (6522)
VR Variable
Resistor
Z80 a
commonly used 8 bit microprocessor
1MHz 1
Megahertz – usually refers to the interface bus running at that
speed
1MhzE Strobe
to which the processor is synchronized
when
accessing "slow" devices such
as 6522 VIA and 1Mhz bus
2MhzE Strobe
to which the processor is synchronised
when
accessing "fast" devices such
as ROM and DRAMs.